After receiving the necessary documents and project presentation, our team will try to review your request as soon as possible, and leading experts will offer the best options for project funding.
Beyond the aging infrastructure and rising operational costs of old LNG facilities, there lies a compelling case for embracing technological advancements and industry best practices.
Properly organized modernization unlocks the potential to optimize LNG plant efficiency, reduce emissions, comply with stringent regulations, and ultimately enhance profitability. If you need financing for a major project in the oil and gas industry, including raising long-term loans from private investors, please contact GCAM Investment Group for details.
Understanding LNG plant modernization
Modern LNG plants play a pivotal role in the liquefaction and storage of natural gas, facilitating its safe transportation and distribution across global markets.These expensive and technically complex facilities carry out a multi-step process that transforms natural gas into a liquid state, reducing its volume significantly for efficient shipping.
Utilizing cryogenic cooling and compression technologies, LNG plants decrease the volume of natural gas by approximately 600 times, enabling cost-effective transportation for many thousands of kilometers from centers of production. Given the engineering complexity and potential hazards of this technology, new plant construction costs investors billions of euros, and regular equipment upgrades require hundreds of millions to maintain high efficiency and safety of key processes.
Typical problems of obsolete LNG infrastructure
Many existing LNG plants have been operational for decades and may face various issues related to aging infrastructure.Outdated equipment, pipelines, storage tanks, and other components can result in inefficiencies, increased maintenance costs, and potential safety risks. Moreover, advancements in digitalization, automation, and data analytics offer new opportunities for enhancing the efficiency of LNG plants. With the global focus on reducing greenhouse gas emissions and transitioning to cleaner energy sources, LNG companies must also adapt to stricter environmental standards.
Table: Obsolete LNG infrastructure faces various problems that hinder its operational efficiency, safety, and environmental performance. Here are some issues with relevant facts and figures.
Issues | Brief description |
Low energy efficiency | Old LNG plants may lack advanced liquefaction technologies, resulting in higher energy consumption per unit of LNG produced. For example, older plants may have specific energy consumption rates of around 0.05-0.07 kWh/m³ of LNG, while modern facilities can achieve rates as low as 0.03 kWh/m³ of LNG. This inefficiency leads to higher operational costs and increased greenhouse gas emissions. |
Aging infrastructure | Over time, the infrastructure of LNG plants can deteriorate, impacting their reliability and safety. Outdated pipelines and storage tanks often suffer from corrosion, leakage, and structural weaknesses. According to several industry reports, the average lifespan of an LNG tank is around 30-40 years. Beyond this period, maintenance costs increase significantly, and the risk of failures or accidents rises. |
High maintenance costs and downtime | Obsolete LNG plants often require frequent and costly maintenance due to outdated equipment. Unscheduled downtime for repairs can disrupt production schedules and reduce operational efficiency. Studies suggest that outdated facilities experience downtime rates of 2-4% per year, resulting in lost revenue and reduced competitiveness. |
Limited production capacity | Older LNG facilities may have limited production capacities due to design constraints and inefficient technologies. Plants built in the 1970s and 1980s typically have capacities ranging from 2 to 6 million tons per year. In comparison, modern plants can exceed 10 million tons per year, meeting the growing demand for LNG more effectively. |
Higher emissions and environmental impact | Outdated LNG plants often emit higher levels of greenhouse gases and pollutants due to less efficient combustion and limited emission control measures. The carbon intensity of LNG production varies significantly, with older plants emitting around 0.25-0.35 tons of CO2 equivalent per ton of LNG, compared to 0.15-0.20 tons in modern facilities. |
Safety risks | Older LNG plants often face safety risks associated with outdated safety systems, inadequate emergency response, and aging infrastructure. Experts indicate that older facilities have higher incident rates and safety-related accidents compared to newer facilities, posing risks to personnel, nearby communities, and the environment. |
Limited flexibility | Obsolete LNG plants lacks the flexibility to adapt to changing market dynamics, such as different gas compositions or emerging LNG trading patterns. They may struggle to handle new gas sources or adjust production volumes efficiently. |
These typical problems of existing LNG plants highlight the urgency for modernization to address inefficiencies, safety concerns, environmental impact, and operational limitations. Upgrading infrastructure, adopting advanced technologies, and implementing best practices can transform obsolete infrastructure into more efficient, safer, and sustainable.
Importance of modernization: enhancing efficiency, safety, and economic performance
Modernization is of great importance for all links of the LNG infrastructure, ensuring they remain highly efficient, safe, sustainable, and economically viable.By embracing modernization, LNG companies can optimize their current operations, improve safety, reduce emissions, and enhance economic performance, making them more competitive in the dynamic global market.
By upgrading equipment and technologies, LNG plants can achieve the benefits listed below.
Improved production efficiency
Modernization measures, such as advanced process control systems, automation, and digitalization, optimize key LNG plant operations, resulting in enhanced efficiency and increased gas production capacity. These improvements usually lead to reduced operational costs, improved profitability, and better economic performance for LNG plant operators.Enhanced safety measures
Modernization initiatives prioritize the implementation of advanced safety protocols, monitoring systems, and emergency response mechanisms. By adopting these cutting-edge technologies, LNG companies can mitigate risks, prevent accidents, and ensure the safety of personnel and surrounding communities, thereby protecting their reputation and avoiding financial losses.Reduced environmental footprint
LNG plant modernization supports environmental sustainability goals by incorporating cleaner technologies and emission reduction strategies. Upgrades may include more efficient liquefaction processes, renewable energy integration, and the adoption of carbon capture and storage (CCS) systems. These efforts contribute to minimizing CO2 emissions, reducing the carbon footprint of LNG production. Aligning with strict environmental regulations can positively impact project financing by attracting investors who prioritize sustainable initiatives.Compliance with industry standards
Modernization is crucial for LNG plants to comply with evolving regulatory and industry standards. Meeting stringent safety, environmental, and quality requirements ensures operational legality and also facilitates further financing by instilling confidence in stakeholders.LNG plant modernization often involves significant capital investments.
Therefore, addressing economic performance and securing project financing should be considered as essential aspects. Demonstrating improved efficiency, safety enhancements, and sustainability measures resulting from modernization efforts attracts private investors, banks and financial institutions. Additionally, emphasizing the potential return on investment, cost savings, and long-term profitability can enhance the feasibility and attractiveness of LNG infrastructure modernization projects.
Key steps for successful LNG plant modernization
Modernization of large industrial facilities in each case is individual in nature, and is developed taking into account the specifics of a particular facility, the project budget, the scope of work and the needs of the customer. Typically, this process includes project planning, financing, equipment and technology optimization, related infrastructure development, staff training, O & M issues.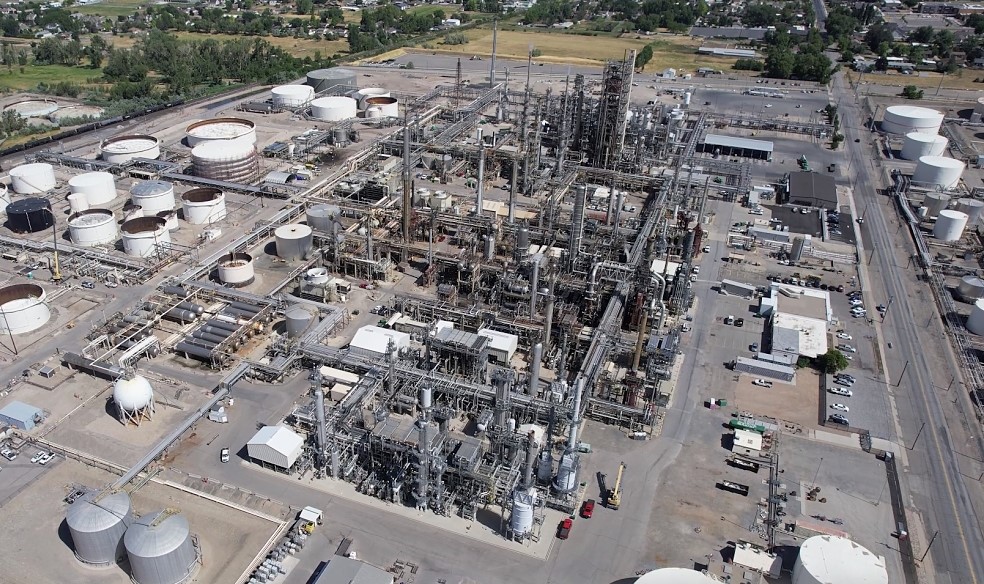
#1 Plant assessment and planning: setting the foundation
To start the LNG plant modernization process, a comprehensive plant assessment is important. This involves evaluating the existing infrastructure, equipment, and processes. Project team must identify areas for improvement and define goals and objectives for the modernization. This includes feasibility studies, cost-benefit analyses, and engage relevant stakeholders to ensure a well-informed and strategic approach.#2 Technological upgrades: optimizing facility performance
Modernization entails embracing new technologies to enhance LNG production performance and economic efficiency. This requires to explore various modernization techniques, such as advanced process control systems and digitalization. These innovations can optimize key process parameters, minimize energy consumption, reduce emissions, and improve overall operational reliability.#3 Infrastructure development: increased capacity and improved logistics
Modernization often involves upgrading LNG plant infrastructure to accommodate increased production capacity and streamline logistical operations.Project team must consider appropriate modifications to LNG storage tanks, pipelines, loading and unloading facilities, and associated equipment. This may require adopting innovative design principles, utilizing advanced materials, and optimizing layouts to maximize efficiency, safety, and reliability. Addressing bottlenecks and optimizing flow patterns can minimize downtime and improve operational flexibility.
#4 Safety and compliance upgrades for sustainable operation
Enhancing safety measures and ensuring full compliance with regulatory requirements are paramount in LNG plant modernization.This includes implementation of modern safety systems, emergency response mechanisms, and process safeguards. Advanced risk assessment methods are important to identify potential hazards and mitigate them effectively. Modernization must be carried out according to industry standards and regulatory guidelines to maintain a safe working environment, protect personnel, and meet legal obligations.
#5 Training and workforce development for effective operation
Successful modernization goes far beyond technology and infrastructure.It also involves equipping the workforce with the necessary skills and knowledge to operate and maintain innovative systems.
Project team must develop training programs that cover new technologies, operational procedures, and safety protocols. It also includes a culture of continuous learning and employee involvement in the modernization process. By empowering the workforce, LNG companies can ensure smooth transition, minimize operational disruptions, and maximize the benefits of modernization efforts.
By following these five steps, LNG plant operators can execute a successful modernization plan that optimizes facility performance, enhances safety and compliance, improves infrastructure, and empowers the workforce.
Each step plays a vital role in creating a resilient, efficient, and sustainable LNG plant for the future business success.
Looking for professional support for your investment project?
Contact our team for details.