After receiving the necessary documents and project presentation, our team will try to review your request as soon as possible, and leading experts will offer the best options for project funding.
As a trusted international partner, the company GCAM is ready to offer tailor-made financial and engineering solutions around the world.
The chemical industry is very competitive.
The trade in chemical products is international and companies are forced to compete with foreign manufacturers both in domestic markets and abroad.
Currently, in many industries there is a tendency towards a reduction in the number of manufacturers and an increase in production volumes. A company without reliable sources of raw materials or the technological knowledge required to achieve competitive manufacturing costs cannot survive in the global market.
The improvement of chemical production largely depends on technical advances and scientific knowledge.
Few chemical plants use their own technology, but the vast majority of companies prefer technology dependence in order to save significant R&D funds.
Chemical technology is dynamic and constantly evolving, so technological processes quickly become obsolete.
However, not all chemical plants quickly become obsolete.
For example, equipment for the production of inorganic chemicals, where technology changes slowly, can last more than 20-30 years. Some ammonia and sulfuric acid plants built in the 1950s continue to operate today with minor technology changes.
But in general, chemical equipment has a shorter service life compared to, for example, equipment in the mining industry.
This is partly due to the fact that the components of chemical equipment are susceptible to corrosion processes. In some cases, construction of a new chemical plant or production line using innovative technologies is much more profitable than modernization.
Chemical plant construction: what to consider?
In addition to finding a source of financing and tax optimization of the project, at the very beginning the project initiator must decide whether the new chemical plant will operate within the existing enterprise or should be an independent legal entity.If the second option is chosen, the first step will be to decide on the form of this new legal entity (limited liability company or joint stock company), as well as the registration of the legal entity.
If you are looking to expedite the start of a new company, it may be much more advisable to acquire an already registered company. You can always get detailed advice from GCAM specialists.
Choosing a place for construction
The next stage of the investment process is the selection of the location of the production facility.Depending on the specific chemical industry, easy linkages to both raw material sources and markets can be critical to achieving high profitability.
Factors influencing the choice of site for the construction of a chemical plant:
• Convenient plot of land for complex structures and equipment.
• Favorable hydrogeological, topographic and climatic conditions.
• Availability of readily available raw materials required for the chemical process.
• The minimum cost of preparation of the construction site and infrastructure.
• Safety of production for the environment and the population.
• Access to roads, railways and / or waterways.
• Access to potential chemical product markets.
• Availability of cheap fuel and energy.
• Supply of industrial water to a chemical plant.
• Collaboration with the local community.
After choosing the construction area, the engineering team looks for construction sites for each of the industrial facilities envisaged by the project.
This requires consideration of factors such as site size, terrain, convenience and safety.
Construction planning requires the involvement of experienced specialists in various fields in order to take into account all possible factors that can affect the project. Miscalculations at this stage can lead to additional financial costs and missed deadlines.
For example, unsatisfactory hydrogeological conditions may require the use of expensive supports and deep concrete foundations.
Also, the problem of access to labor should not be overlooked. In the case of a chemical plant construction, a skilled workforce is considered an important factor (companies can always consider working with local recruiting agencies).
For this reason, it is advisable to locate chemical enterprises near technical universities.
When looking for a suitable site to build a chemical plant, it is important to consider the benefits of investing in the special economic zones that are currently booming.
Also, do not forget about tax benefits, for example, exemption from real estate tax for a certain period. At this stage, it should be remembered that the planned activity must correspond to the municipal development plans.
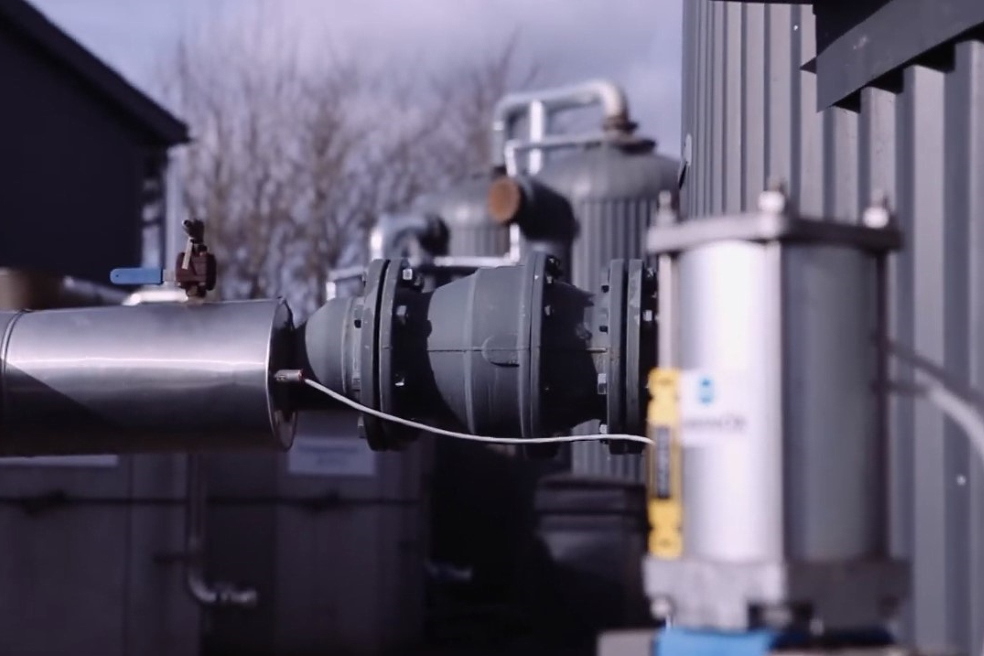
Determination of the optimal production capacity
The planned volume of production and the range of chemical products is determined by the investment plan.Further technical assignments performed by the general contractor are based on the capacity of the chemical plant and specific technological processes selected by the customer in consultation with the engineers.
The construction of modern chemical plants is carried out in such a way as to ensure the possibility of simple and quick modernization, expansion of production or changes in technological processes without significant investment costs.
Our team takes into account numerous factors, such as the current and projected demand for chemical products, the availability and prices of raw materials and fuels, changing sales policies, the stage of market development and others.
Detailed analysis helps our customers make informed decisions with maximum benefit.
Environmental aspects
Environmental analysis is performed to predict the impact of the construction of a chemical plant on the environment and human health.The operation of most chemical facilities poses a certain risk, therefore, technological issues must be worked out in detail.
Environmental analysis for the construction of a chemical plant includes the following stages:
• Assessment of the initial parameters of the environment.
• Assessment of the location of a chemical plant and its impact on the environment, taking into account the specific parameters of technological processes and their intensity.
• Establishment of clear boundaries of the ecological system (area) and specific objects that are at risk as a result of the construction and operation of the enterprise.
• Verification, which involves checking the validity of the data received.
• Development of a plan to minimize the environmental impact of chemical production.
It is well known that large-scale chemical production affects the soil layer in the construction area, negatively affecting vegetation, fauna, the quality of ground and surface waters, air composition and ecological balance in general.
GCAM's team works with leading European chemical engineering specialists to make production processes cleaner and safer.
Together with our partners, we actively use our experience and advanced technological solutions for the construction and modernization of chemical plants around the world, including the EU countries, North Africa, East Asia and Latin America.
Legal aspects
The next step is to answer the question of what legal status and land ownership would be most beneficial for the project initiator.In this context, it is worth considering the type of chemical production, the duration of the planned investment, the scale of construction and other aspects.
In the engineering design of a chemical plant, attention should be paid to the legal requirements for environmental protection and waste management. This issue is important already at the design stage of the planned investment, regardless of whether we intend to use hazardous substances in production or not.
It is important to remember that when planning the size and layout of industrial buildings, we must take into account numerous legal regulations governing the storage and disposal of hazardous chemicals, as well as safety regulations.
Chemical engineering: our professional services worldwide
Currently, many chemical plants in developing countries require deep modernization.Moreover, some companies are actively looking for partners for the construction of new enterprises due to the reorientation to innovative products and new markets.
GCAM offers a full range of financial and engineering services, including chemical plant investment project planning, project management, process development and engineering design of all types of equipment.
Chemical engineering experts are exploring new methods of chemical production, introducing advanced equipment and technologies to improve product quality and purity, and reduce the energy intensity of processes. The design process takes into account the practical experience of the best European and American factories, as well as the technical achievements of researchers.
Choice of chemical production technology
Comparison and selection of the optimal technology is an important step on the way to the construction of a new chemical plant.Each stage of the technological process, be it filtration, drying or packaging of the finished product, requires an individual analysis.
When choosing a technology, we focus on the needs of the customer, available raw materials, the desired quality of the finished product (chemical purity, humidity, etc.). Since the cost of raw materials makes up a significant part of the production costs in the chemical industry, we are always ready to offer you valuable alternatives.
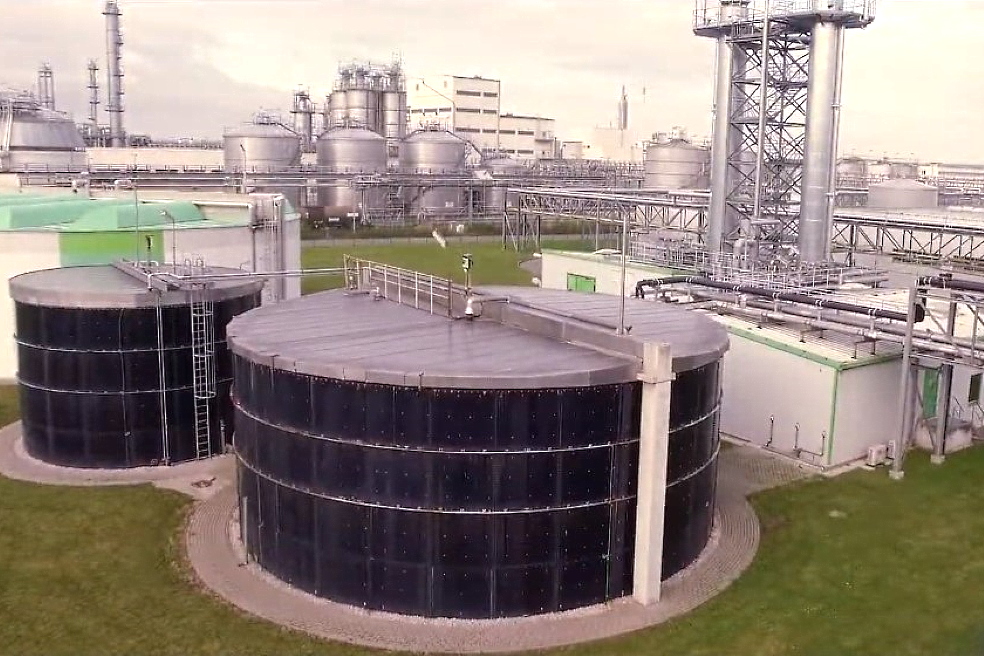
Choosing a production technology, we are guided by the current rules and standards of safety, health and environmental protection requirements, etc.
As a result of painstaking work, you will get a modern plant that fully meets the requirements of the investment project and the interests of your business.
The cost of chemical products depends on the following factors:
• Costs for raw materials, packaging, auxiliary materials.
• Energy costs, including fuel and energy costs.
• Salaries of engineers and workers supporting the process.
• The total cost of maintaining the operation of the enterprise.
• Depreciation costs and other items.
Experts distinguish chemical production of continuous type and batch type, which operate continuously or in cycles.
It should be understood that the use of a continuous method is possible only if there is a reliable source of raw materials with constant specified properties, automatic control and maintenance of key production parameters, reliable and uninterrupted operation of equipment.
Continuous chemical production has a number of advantages, including process stability, ease of setting production parameters and complete automation, as well as savings due to the absence of frequent starts and stops of equipment.
But this type of production is suitable mainly for large chemical plants, while small-scale production is better carried out in cycles.
The impact of increasing plant capacity on production costs and capital expenditures should be analyzed. Cost components such as raw material costs are almost independent of the scale of production. An increase in production capacity is usually associated with an increase in equipment capacity. This leads to a decrease in energy consumption per unit of production, as well as heat loss to the environment.
Consequently, scaling reduces production costs.
When choosing a technology, it is important to analyze competitors and assess the feasibility of introducing certain approaches.
Our team will help you make the right choice based on many years of experience in financing industrial projects.
Construction of large chemical plants under the EPC contract
Today, the EPC contract is becoming an increasingly popular way to implement large investment projects in various industries.The construction of a chemical plant under an EPC contract provides the project initiator with many benefits, ranging from the best practices of the general contractor to the minimization of project management efforts, which is transferred to our team.
At the stage of engineering design, our specialists solve all technical, environmental and other problems of future production.
Taking into account the latest achievements of science at this stage, equipment is selected, a technological scheme of production is developed, building structures are designed, a technological scheme is created, and the layout of equipment is selected.
The issues of energy supply, automation and mechanization of production, estimates or specifications for the corresponding equipment are compiled.
GCAM with partners are ready to provide support in financing of large projects, expansion or modernization of chemical plants. We have many years of practical experience in engineering services in many countries around the world.
We are also ready to provide you with flexible project financing schemes, including investment lending for the construction of chemical plants.
Contact our consultants to find out more.