After receiving the necessary documents and project presentation, our team will try to review your request as soon as possible, and leading experts will offer the best options for project funding.
Taking into account that 71% of the Earth's surface is water, it becomes clear that business is interested in the transition from the traditional method of transporting gas through pipelines to liquefied natural gas (LNG).
The use of LNG as a source of energy supply is becoming more and more profitable in many regions of Europe and the world.
Therefore, the technology of liquefaction, transportation, storage and regasification of liquefied natural gas is currently being actively developed.
Using gas as a fuel source is less harmful to the environment than other fossil fuels such as coal or oil.
LNG imports also enable many companies to diversify their energy sources and ensure energy security for many years to come.
Compared to the early 2000s, dozens of new countries began to import liquefied natural gas for their own needs, expanding the geography and variety of markets. In some countries, such as South Korea and Japan, LNG fully covers gas needs, while other countries use LNG imports to bridge the gap between local production and peak economy needs.
LNG is a valuable tool for transporting gas to regions not served by gas pipelines. It can become an additional source of gas supplies for millions of consumers if the construction of new regasification terminals and related infrastructure is ensured.
Table: Global LNG trade volume from 2009 to 2019 (billion cubic meters per year)
Year | 2008 | 2009 | 2010 | 2011 | 2012 | 2013 | 2014 | 2015 | 2016 | 2017 | 2018 | 2019 |
Volume | 235 | 250 | 302 | 328 | 325 | 327 | 334 | 337 | 358 | 393 | 431 | 485 |
LNG is an odorless, non-toxic, non-flammable and non-corrosive liquid that must be stored at very low temperatures.
Spilled LNG evaporates quickly as methane, leaving no residue on soil or water.
Since liquefied natural gas weighs half as much as water, gas spilled in the sea floats to the surface and then evaporates into the air. In the event of an emergency leak of liquefied natural gas into water or land, no environmental pollution occurs.
The main stages in the life cycle of liquefied natural gas include:
• Liquefaction of natural gas from its gaseous form, which is carried out in an LNG plant by cooling to about - 160 ° C. During condensation, the gas is compressed to almost 1/600 of its original volume. LNG plants are located primarily in gas exporting countries.
• Transportation by sea. LNG is transported by special vessels called methane carriers inside special tanks, where the gas is safely stored in the liquid phase at low temperatures.
• Loading and unloading of methane carriers. For loading and unloading LNG carriers, it is necessary to build special port facilities with powerful pumps and storage tanks.
• LNG regasification. Regasification terminals are being built for the controlled conversion of LNG to the gaseous state. Here, the gas is stored in tanks, and when consumers require fuel, it expands to a gaseous state and is pumped into gas pipelines. LNG can be transported overland by road tankers and rail tank cars.
There are currently more than eight dozen LNG regasification terminals around the world.
Particularly in Europe, dozens of terminals have been set up along the coasts of Belgium, France, Poland, Greece, Italy, Spain and the UK.
According to the International Energy Agency, the number of regasification terminals and LNG carriers will grow steadily in the coming decades. In particular, they will be needed by American exporters, who are constantly increasing production of LNG from natural gas from shale fields. According to these forecasts, in 2040 the global fleet of methane carriers should approach a thousand units.
Engineering design of LNG regasification terminals is a comprehensive professional service that requires the involvement of engineering companies with rich practical experience and advanced technologies.
GCAM and its partners offer financing and design services for LNG infrastructure around the world, using European innovation and high quality equipment from renowned manufacturers.
Technical aspects of transportation, storage and regasification of LNG
To clearly understand the technological aspects of LNG handling and engineering design of LNG regasification terminals, we suggest looking at its life cycle from liquefaction to end use.The LNG industry is heavily exposed to the same risks that exist in any industrial activity. Specialists will design all types of equipment for LNG transportation, regasification and storage, offering individual technological solutions for each project.
Natural gas, containing 98% methane, in liquefied form takes only 0.17% of the volume of the same amount in the gaseous state.
This corresponds to approximately 1/600 of the gas volume.
Hundreds of times the volume reduction is a significant advantage during transportation and storage.
The natural gas liquefaction process involves purification by separating certain components such as dust, carbon dioxide, hydrogen sulfide, helium, water and heavy hydrocarbons, which can cause difficulties in converting a gas to a liquid. The next step is condensation at a pressure close to atmospheric.
After pretreatment to meet regulatory quality requirements, the natural gas is liquefied at a temperature of about −162 ° C (the boiling point of LNG depends on its composition and ranges from −166 ° C to −157 ° C). This technically complex stage allows the company to prepare gas for storage and transportation to the consumer. By keeping the temperature extremely low, LNG does not need to be stored under pressure.
It is an environmentally friendly fuel with an octane rating of 130.
Liquefied natural gas is colorless, odorless, and does not cause corrosion of metal pipelines and tanks.
Natural gas (methane), and therefore LNG, is non-toxic and safe for humans.
The density of LNG depends on its composition and ranges from 430 kg / m³ to 470 kg / m³. Therefore, liquefied natural gas floats on water, the density of which is about 1000 kg / m³. Methane is practically insoluble in water.
The density of methane at a low temperature close to condensation (-160 ° C) is approximately 1.75 kg / m³, that is, more than that of air. During spraying, this gas accumulate above the ground. When the temperature rises to -110 ° C (- 113 ° C for pure methane), methane becomes lighter than air and is dispersed by the wind.
If LNG leaks from tankers or pressurized pipelines, it will be released into the atmosphere.
This process is associated with active physical mixing of methane particles with air. Initially, most of the gas will be contained in the released cloud as aerosol.
Then, as a result of mixing with air, the LNG will gradually evaporate, practically without affecting the ecosystem.
LNG industrial infrastructure consists of liquefaction equipment, a loading terminal, methane carriers and LNG regasification terminals, where regasification takes place to a gaseous state.
At terminals, LNG is stored in specially designed tanks. After liquefaction, the gas is transported by LNG carriers to its destination. In turn, the operation of the unloading terminal can be divided into three main stages, including the stage of unloading, storage and regasification to obtain a ready-to-use product.
The unloading step should be understood as an operation when a methane carrier moored in the port of the receiving terminal is connected to the LNG storage tank using a hose. Pumps, located on LNG carriers, transport gas from the vessel's internal tanks to stationary storage tanks.
Tanks must be designed to ensure safe storage of LNG in the cryogenic temperature range.
The regasification stage consists in heating the liquefied natural gas in heat exchangers (evaporators) to convert the LNG into a gas phase with parameters that comply with local regulations and ensure further gas transportation.
The LNG regasification terminal is connected to the gas transmission network, which transfers natural gas to the end consumer after confirmation of its quality parameters.
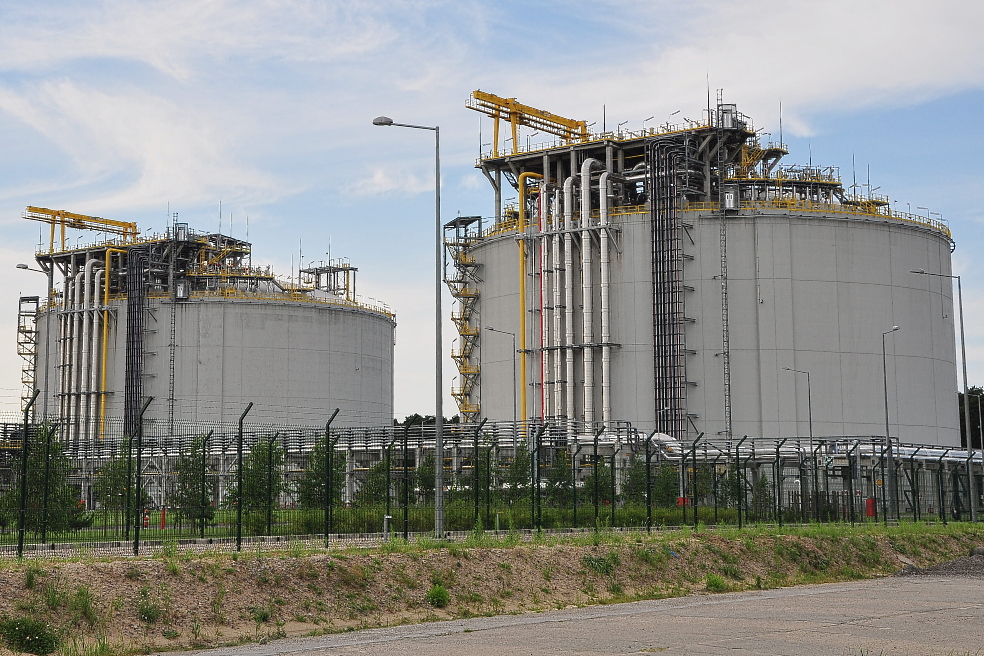
Equipment for storage of liquefied natural gas
It is important for the engineering company to ensure the safe storage of LNG both at the stage of its loading and at the stage of regasification.For this, reliable materials for the manufacture of tanks and devices should be used, as well as an appropriate technical design should be provided at each technological stage.
In the engineering design of LNG regasification terminals, it is most important to choose the right tank design. They vary according to volume, operating pressure, configuration, control systems and standards that define the specific construction technology.
Overall, the LNG tank is structurally similar to a giant thermos mounted on a foundation slab that is properly insulated and heated. The design of the reservoir depends on the geology of the area on which it is built. The tank must be equipped with electronic protection systems to ensure safe operation.
Liquefied natural gas storage tanks are divided into aboveground tanks, semi-underground (semi-submerged) tanks, and underground (submerged) tanks.
The following types of LNG tanks are often used in engineering practice:
• Single containment tank without external protective casing (SCT). The outer casing is made of carbon steel, and the inner one is made of nickel steel, which does not change properties at low temperatures. The tank is placed in a pit to ensure safety in the event of a leak of liquefied gas into the environment.
• Steel tank with additional double containment tank (DCT). Essentially, this structure is an SCT surrounded by a special open top prestressed reinforced concrete casing to ensure the safe storage of LNG in the event of a breach in the internal reservoir.
• Steel tank with an outer full containment tank (FCT). Equipment of this type is similar to the previous two types, with the difference that the structure of the external tank is a ring and a domed roof made of prestressed reinforced concrete.
The most commonly used materials include austenitic stainless steels, aluminum alloys, and nickel alloys with specific toughness at temperatures below - 60 ° C.
Polymeric materials such as glass fiber reinforced epoxy resins can also be used.
The steel from which the internal LNG tanks are made must be crack-resistant at very low temperatures and also have the ability to limit crack propagation. This steel has a low content of phosphorus, sulfur and carbon, which avoids the reduction in toughness in the heat-affected zones during welding.
From the inside, the tanks are sealed with a thin corrugated membrane.
Due to its shape, such a reservoir can easily withstand stresses arising from temperature differences between the environment and the stored liquefied gas.
Aluminum is used for the construction of suspended roofs for internal tanks.
External tanks are usually made of carbon steel or prestressed reinforced concrete. The correct selection of building materials and the use of appropriate bonding methods determine the safe and long-term operation of LNG tanks.
Thermal insulation is a critical element of the LNG tank. The insulating materials used should provide the lowest possible thermal conductivity. The bottom of the tank is insulated with foam glass or other suitable material. The space between the cylindrical part of the inner and outer tanks can be filled with expanded perlite. Fiberglass or expanded perlite is used to provide thermal insulation for the roof of the inner tank.
LNG carrier unloading technology
Pumping gas from LNG carriers into stationary tanks of the LNG receiving terminal at the port is one of the most important elements of the liquefied gas transportation system.This process is carried out using powerful pumps on board the tankers.
Each LNG carrier is equipped with two types of pumps. These are high-capacity main pumps used to transfer LNG to storage tanks, and smaller pumps that keep storage tanks cool.
The capacity of these devices can exceed 1000 m³ / h for the main pumps and 50 m³ / h for the auxiliary pumps. The storage capacity of a typical LNG carrier is about 130-150 thousand cubic meters. Pumping this amount of liquid will require about 3000 kWh of energy. Almost all of this energy is converted to heat and absorbed by the gas.
This amount of energy causes the stored liquid to heat up by 0.5 ° C.
The vapors generated during boiling have a higher energy than the cryogenic liquid remaining in the tank, so its temperature is stabilized.
Thus, in order to maintain a constant temperature, part of the transported LNG must be vaporized.
Liquefied natural gas is transported through pipelines to a system of stationary storage tanks located at a distance of 1000-1500 m. The pipelines located on racks are usually equipped with compensators that absorb mechanical stresses arising from temperature differences. The pipelines are thermally insulated with polyurethane or vacuum using a pipe-in-pipe system.
The unloading area with the storage tank of the LNG receiving terminal is connected by a system of two unloading pipelines. According to the technology, the unloading process is preceded by additional cooling of the pipeline. This is usually accomplished by sending a small amount of LNG to the offloading area through one pipeline and returning it to the preparation area through a second pipeline.
The discharge line must be well insulated.
The amount of heat that penetrates each square meter of the surface of this pipeline is extremely small.
However, taking into account its many kilometers length, the total heat losses turn out to be significant. The amount of methane evaporated as a result of heat loss for every 1 km of the length of such a pipeline, depending on the type of thermal insulation, can reach several tons per hour.
Vapors returning to LNG carriers affect the boil-off rate. When a tanker unloads at the receiving terminal, a significant amount of liquefied gas is squeezed out of its tanks in a very short time, which creates a local negative pressure.
To counteract this and maintain a constant operating pressure in the tanks, the squeezed out LNG is replaced with methane.
Some of the gas required to fill the tanks is covered with vapors that have evaporated during the trip, and the rest must be supplied from the outside. This is called BOG (boiling gas). At the initial stage of unloading LNG carriers, after connecting the unloading arms to the ship's manifolds, BOG is used to cool the unloading arms and auxiliary devices at the berth.
This stage uses a condensate tank located on the unloading platform and a chiller, in which the cold source is LNG. The same devices are used to ensure that the vapors returning to the tanker are sufficiently cold.
Unlike the unloading pipeline, this pipeline does not maintain a low temperature, so the gas flowing through it must be additionally cooled to the appropriate temperature before it enters the tanker.
Liquefied natural gas regasification process
Regasification is the final stage in the life cycle of liquefied natural gas.Here, the liquid product is converted to a gaseous state and pumped into the onshore gas pipeline network.
LNG regasification is performed in three sequential stages:
• Natural gas is transported by sea with LNG carriers and discharged into stationary tanks in a liquid state. LNG can be stored in the port for a long time and used in accordance with the changing needs of consumers.
• Regasification involves heating LNG to temperatures above 0 ° C. This process is carried out at a pressure of about 60-100 bar. Heating is carried out in groups of heat exchangers using seawater as a heat carrier. This is the most energy efficient method when water of the required quality is available. The problem with this type of heating remains the difficulty of using seawater due to the large amount of impurities and its high corrosiveness. In the event of an accident in the heat exchangers, the gas is directed to a backup evaporator, which uses the combustion of part of the fuel to generate the required heat energy.
• At the exit from the LNG regasification terminal, methane gas is purified and processed to meet quality standards. Processing can involve changing the calorific value of the product by adding nitrogen, butane, or by mixing with other gases. An important step after regasification is to treat the gas with an odorant to ensure safe handling of the gas.
The engineering design of LNG regasification terminals must take into account the specific needs of the customer.
Regasification can be carried out both at traditional onshore terminals and on autonomous floating platforms. Floating regasification units have the advantage of mobility and can create new markets for LNG.
In addition to the availability of gaseous fuels, the benefits of LNG regasification can be derived from the energy released. The cold released when methane is converted from liquid to gas is used to produce oxygen and nitrogen from the air.
Companies can reap the most significant benefits by building LNG regasification terminals in close proximity to metallurgical plants or other industrial facilities.
Main equipment for LNG regasification
The engineering design of LNG regasification terminals relies on the selection of the most suitable equipment, including cryogenic tanks, evaporators, reducers and metering equipment.The list of major equipment for LNG regasification includes:
• Cryogenic storage tanks for liquefied gas. These tanks of the appropriate type, volume and design provide long-term storage of LNG, minimizing the potential risks in case of emergency situations at the terminal.
• ORV, SCV or other vaporizers that are specifically designed for the controlled conversion of liquid LNG to a gaseous state with high performance and safety.
• Reduction station. This part of the LNG regasification terminal is responsible for reducing the pressure of gaseous methane to the required parameters, as well as controlling the supplied gas according to various indicators.
• Odorization equipment. Since LNG is odorless, suppliers must give it a specific pungent odor for safe use.

Among the most important equipment can be called evaporators, where the most complex process of gas phase transformation takes place.
LNG regasification terminals usually have two types of evaporators, namely ORV or SCV.
ORV (open rack vaporizer)
ORV, or open rack evaporators, are seawater heated heat exchangers.In these heat exchangers, seawater flows by gravity through galvanized aluminum pipes, heating the LNG flowing around the panels.
The water flowing out of the aluminum pipes accumulates in a tank, from where it is discharged into the sea through a pipeline.
Before use in heat exchangers, seawater should be cleaned of all types of suspended matter or solid impurities. It must also meet strict quality requirements, that is, it must not contain heavy metals, and the pH of the water must be in the range of 7.5-8.5 with a minimum content of chlorine ions. It is also important to ensure that the sea water temperature is maintained above + 5 ° C.
Water discharged back into the sea is usually a few degrees below sea temperature. These are very insignificant figures in the general quantitative balance and should not pose a threat to the environment. To prevent the growth of various biological forms inside the pipes, it is necessary to chlorinate the water with low doses of chlorine-containing substances.
Due to their simplicity of technology and low failure rates, ORVs are among the most widely used in LNG regasification terminals in Europe.
Despite the higher construction costs, their operating costs are relatively low among all similar systems.
SCV (submerged combustion vaporizer)
SCV, or Submerged Combustion Evaporators, are heat exchangers that use the temperature of the exhaust gas.The principle of operation of these heat exchangers is to burn a gas stream, often using one large burner. The hot exhaust gases then pass through steel pipes immersed in a water bath. The combustion products are released into the atmosphere after cooling.
Using one large gas burner in this system instead of several smaller burners is associated with greater efficiency and lower NOx and CO emissions.
Other types of evaporators for LNG regasification terminals are used less frequently.
The most famous are STV (shell and tube vaporizers), CHP - SCV (combined heat and power unit - submerged combustion vaporizers), AAV (ambient air vaporizers) and AAV - HTF (ambient air vaporizer - heat transfer fluid).
In each case, the construction of LNG regasification terminals requires an individual approach, taking into account the specific conditions of the project, the requirements of stakeholders, the project budget and the anticipated commissioning time.
Financing and engineering design of LNG regasification terminals
The transportation of liquefied natural gas by waterways is relevant all over the world.Using the existing port infrastructure, investors can develop networks of LNG regasification terminals in existing ports and consider additional locations in new coastal areas.
Despite the many advantages associated with the development of the LNG market, the options for implementing a multimodal supply chain are currently limited. The main obstacles to development include underdeveloped rail infrastructure in many regions of the world, non-navigable river sections, high costs during the implementation phase of infrastructure projects and insufficient awareness of the authorities about new solutions related to LNG transportation.
However, implementing small, customized LNG solutions can bring significant benefits to your business.
GCAM with partners offers all types of financial, engineering and advisory services related to the development of liquefied natural gas chains.
We develop investment and technological schemes, select and supply advanced equipment, perform installation and ensure the smooth operation of LNG regasification terminals for your business.
Engineering services include, but are not limited to:
• Engineering design, construction, maintenance and modernization of LNG regasification terminals under the EPC contract.
• Engineering design, construction, maintenance and modernization of LNG plants around the world on a turnkey basis.
• Purchase, supply, installation, maintenance and replacement of gas compressors for liquefied natural gas plants.
• Design and construction of compressor stations for gas pipelines.
• Project financing of oil and gas projects.
We work with our partners under an EPC contract, concluding an exclusive contract for engineering design, equipment supply and construction of a finished object in the required time frame.
A single general contractor gives the customer significant benefits to the customer in the form of a single center of responsibility. The comprehensive professional approach of our team guarantees compliance with strict standards, as well as the optimal cost and timing of the project.
We have participated in the implementation of strategic projects in the United States and countries of Europe, Latin America, Africa and Asia.
Among our partners are many famous engineering companies and financial institutions, including the largest banks in Spain. Our experience is the key to the success of your oil and gas project.
If you are planning an investment in an LNG regasification terminal, please contact GCAM consultants for additional information.