After receiving the necessary documents and project presentation, our team will try to review your request as soon as possible, and leading experts will offer the best options for project funding.
These industrial complexes play a crucial role in producing essential nutrients that enhance soil fertility and crop yields, ensuring global food security and sustainable agricultural practices.
However, the construction of such plants requires substantial investment, often necessitating public-private partnerships, international funding, and strategic collaborations to ensure long-term viability and the adoption of advanced technologies for efficient and environmentally friendly production processes.
Adequate financing and investment in mineral fertilizer plant construction are vital to support global agricultural development and address food scarcity challenges for a thriving future.
GCAM Investment Group offers long-term debt financing for the construction of mineral fertilizer plants in Europe, the USA, Latin America, India, the Middle East and other regions of the world. We are always happy to provide you with advice and familiarize you to our services.
Planning, financing, construction: main phases of a project
The production cycle of mineral fertilizers usually includes several typical industrial plants, each of which performs certain stages of the production process.For example, plants for the production of potash fertilizers are usually close to potash ore deposits, since the basis of the production cycle in this case is the processing of potash ores, followed by purification and granulation of products.
In particular, various production cycles may include plants for the production of nitric acid, phosphoric acid, enterprises for the production of microfertilizers and their components, plants for mixing and packaging mineral fertilizers, and other facilities. The production of the main marketed products for the global mineral fertilizer market is usually carried out at different enterprises, sometimes geographically dispersed at considerable distances from each other, which is often determined by access to natural resources and supply chains.
Constructing a mineral fertilizer plant in the current economic realities requires careful planning, strategic financing, and adherence to to increasingly stringent standards.
As in any other large investment project, there are four main phases here, namely the planning phase, the search and attraction of capital, the construction stage, and the O&M phase that follows it.
Table: Brief description of the key phases of the development of the fertilizer plant project.
Project phases | Description |
Planning phase | |
a. Feasibility study | Before embarking on mineral fertilizer plant construction, conducting feasibility study is crucial. This study assesses current market demand, raw material availability, technology selection, potential environmental impact, and overall financial viability. |
b. Site selection | Choosing an appropriate plant location involves factors such as proximity to raw material sources, transportation infrastructure, availability of utilities, and compliance with zoning and environmental regulations. |
c. Permitting stage | Obtaining necessary permits and ensuring compliance with local, regional, and national regulations is essential for large investment project of this type. This includes environmental impact assessments, land use permits, and safety compliance. |
d. Design and engineering | Collaborating with experienced engineering firms to design the facility layout, technological process flow, and equipment selection is also important. It should align with production capacity, product quality, and operational efficiency goals. |
Project financing | |
a. Capital investment | Estimating the total capital investment required for mineral fertilizer plant construction involves costs for land acquisition, plant infrastructure development, equipment purchase, and other. Attracting financial resources through long-term investment loans and public-private partnerships is common. |
b. Financial projections | Creating detailed financial projections is essential for attracting investors or securing loans. It should include revenue forecasts, cost analysis, cash flow projections, and return on investment calculations. |
c. Government incentives | Project initiators should carefully explore government incentives, grants, tax breaks, or subsidies available for promoting fertilizer production or supporting environmentally friendly projects. |
d. Risk management | It is critically important to identify and assess potential risks associated with delays, cost overruns, market volatility, and regulatory changes. Appropriate risk mitigation strategies and contingency plans can protect the project's financial viability. |
Construction phase | |
a. Contractor selection | Choosing experienced and reputable contractors who specialize in mineral fertilizer plant construction is also important. Project initiators should conduct evaluations, considering their track record, expertise, and adherence to standards. |
b. Project management | Employing skilled project managers is crucial for overseeing construction activities, coordinating contractors, ensuring timelines, managing budgets, and maintaining quality control. |
c. Safety compliance | In modern construction projects, the safety of workers, local communities and the environment is one of the top priorities. This applies, among other things, to environmental regulations, especially regarding waste management and emissions control. |
d. Quality control and testing | The project teams should implement quality control measures throughout the entire construction process, ensuring adherence to design specifications and standards. Rigorous testing and inspections should be conducted. |
Operation and maintenance | |
a. Staffing and training | A skilled workforce capable of operating and maintaining the fertilizer plant should be recruited and trained. Ongoing training programs should be provided to enhance operational efficiency, safety, and product quality. |
b. Marketing and distribution | Effective marketing strategies should be developed to promote fertilizer products and secure distribution channels. Relationships should be established with agricultural suppliers and distributors. |
c. Continuous improvement | A culture of continuous improvement should be embraced to enhance industrial production processes, optimize resource utilization, and explore innovative technologies. Regular review and update of operational procedures should be conducted to remain competitive in the market. |
As we can see from the table above, constructing a mineral fertilizer plant requires comprehensive planning, rational financing strategies, and diligent execution.
By conducting feasibility studies, securing appropriate financing, and managing the construction process efficiently, businesses can establish a successful and sustainable fertilizer production facility.
Mineral fertilizer plant construction step by step
The actual technical stages of the construction of a mineral fertilizer plant begin with planning the parameters of the future plant, choosing the appropriate technological process and calculating the equipment necessary to achieve the set production goals.The purchase of equipment, civil works and installation that are the most expensive stages of projects of this type, taking away much more than 50% of the budget. For this reason, the selection of technologies and equipment, engineering services, and the contracting of the appropriate contractor should be given top priority.
Equipment selection and purchase
The choice of equipment for a mineral fertilizer plant includes the following tasks:1. Equipment for handling chemical raw materials. This includes conveyors, hoppers, and storage silos for handling raw materials like phosphate rock, potash, and other minerals.
2. Equipment for crushing and grinding. Crushers, mills, and grinding equipment are required to reduce the particle size of the material to a suitable particle size for further processing.
3. Equipment for mixing and granulation. Mixers and granulators of various types and designs are used to combine different chemical raw materials and form granules or pellets.
4. Equipment for drying and cooling. Dryers and coolers are employed to remove excess moisture from the granules and cool them to prevent subsequent clumping.
5. Equipment for screening and classification. Screening equipment for mineral fertilizer production is used to separate the granules based on size or quality specifications.
6. Equipment for coating and packaging. This equipment is used to add different substances to the fertilizer granules, and packaging machinery is required for final fertilizer packaging.
The global market for equipment used in the production of mineral fertilizers is a thriving and dynamic landscape, driven by the global demand for agricultural productivity and sustainability. Leading the pack is China, renowned for its extensive manufacturing capabilities and technological advancements.
Chinese companies such as Sinopec Group have demonstrated real success in producing a wide range of equipment, including raw material handling systems, granulation machinery, drying and cooling systems, and packaging solutions.
Another significant player in the global market is the United States, which boasts a strong agricultural industry and a rich history of innovation. Local manufacturers have established their presence with cutting-edge technologies in areas such as process automation, precision application systems, and advanced control systems. In addition, the United States is home to some of the most successful engineering firms such as KBR, providing comprehensive services for the design and construction of industrial facilities.
Other major equipment manufacturers are Germany (UFT, ThyssenKrupp,), Austria (Christof Industries), India, Great Britain, and a number of other countries.
Construction stage
The actual stage of civil works, as well as the installation and adjustment of equipment following it or carried out in parallel, is the most technically complex, time-consuming, lengthy and expensive stage of the project.These works, depending on the type, scale and location of the project, usually cost from several tens to several hundred million dollars. The duration of this stage varies from a few months for small modular plants to a couple of years for large enterprises.
The construction stage includes the following:
1. Civil works: construction site preparation, foundation construction, structural steelwork, and construction of buildings for various plant sections, including main production units, storage areas, laboratories, and administrative offices.
2. Mechanical installation: installing the machinery and equipment in designated locations, connecting them to utilities (electrical power, water, compressed air), and ensuring proper alignment and integration of each element.
3. Electrical equipment and instrumentation: electrical systems, including power distribution, lighting, and control panels, are installed. Instrumentation equipment, such as sensors, transmitters, and controllers, is integrated to monitor and control the facility.
4. Piping and plumbing: piping networks are installed to transport chemical raw materials, process fluids, and utilities throughout the plant. Plumbing installations include sanitary systems, fire protection, and drainage.
5. HVAC and ventilation: heating, ventilation, and air conditioning systems are necessary to maintain suitable temperatures and air quality within the plant buildings.
Commissioning of the plant
The commissioning is a crucial step that involves thorough testing, inspection, and optimization of the facility before its full-scale operation.It ensures that all systems, equipment, and processes are functioning as intended, meeting safety, quality, and production efficiency standards.
This stage usually includes the following:
1. Testing and calibration: each piece of equipment and system is thoroughly tested to ensure proper functioning. Calibration is performed, and adjustments are made as necessary.
2. System integration: all the mineral fertilizer plant systems are integrated and tested together to ensure smooth communication and operation.
3. Performance optimization: fine-tuning of processes and equipment is conducted to achieve desired production capacity, product quality, and operational efficiency.
4. Training and documentation: facility operators and maintenance personnel are trained on equipment operation, safety protocols, and proper maintenance procedures. Documentation, including operating manuals and standard operating procedures, is prepared.
The commissioning of a mineral fertilizer plant ensures a smooth transition from construction to production, minimizing risks, and maximizing operational performance. It is a critical milestone that ensures the plant's readiness, reliability, and compliance, setting the foundation for sustainable and profitable fertilizer production.
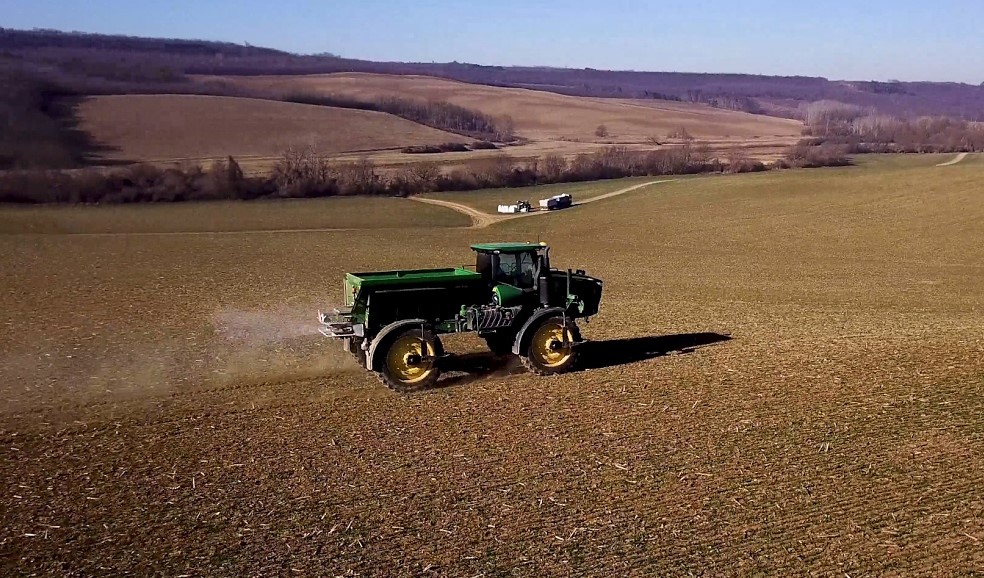
Factors affecting the cost of construction of a mineral fertilizer plant
Projects for the production of fertilizers and their individual chemical components are among the most capital-intensive in the industry, typically starting at several hundred million dollars. The cost of a mineral fertilizer plant can be influenced by various factors.Table: Key factors affecting the final cost of a mineral fertilizer plant.
Factors | Influence |
Plant capacity | The capacity of the facility, measured in terms of annual production volume, can significantly impact the cost. Larger plants with higher production capacities generally require more extensive infrastructure, larger equipment, and higher capital investments. |
Production technology and process design | The choice of technology and process design can have a significant impact on the cost. Advanced and efficient technologies may require higher upfront investments but can result in lower operational costs over the long term. On the other hand, older or less efficient technologies may have lower initial costs but higher ongoing operating expenses. |
Raw materials | The cost and availability of raw materials, such as phosphate rock, ammonia, potash, and sulfur, can impact the overall cost of the plant. Fluctuations in raw material prices can affect project economics. The proximity of the plant to raw material sources can significantly impact transportation costs. |
Infrastructure and utilities | The cost of infrastructure, such as land, buildings, utilities (water, electricity, steam), and waste management systems, can significantly contribute to the overall project cost. The complexity and scale of infrastructure requirements vary depending on the size and location. |
Engineering, Procurement, and Construction contracts | The choice of EPC contractor and the terms of the contract can influence the project cost. In this context, it is important to pay attention to factors such as contractor expertise, general project management, and procurement strategies. |
Regulatory compliance and environmental standards | Compliance with environmental regulations and adherence to safety standards may require additional investments in pollution control equipment, safety measures, and environmental mitigation measures. |
Operating expenses | Labour costs, including wages, benefits, and availability of skilled workers, can affect the construction and operational expenses of the plant. Additionally, ongoing expenses, such as energy consumption, maintenance, and raw material sourcing, can impact the overall cost. |
Market conditions | Market dynamics, including supply and demand factors, pricing volatility, and competition, can influence the cost of establishing and operating a mineral fertilizer plant. Market conditions may affect the financial viability of the project and the return on investment. |
As practice shows, several factors can influence the construction of a mineral fertilizer plant, including the availability and proximity of raw materials, environmental regulations, and infrastructure development for transportation and energy supply. Additionally, market demand, economic feasibility, and government policies and incentives also play important roles in determining the construction and viability of such projects.
Components of the project cost
To ensure accuracy in cost estimation, it is essential to consider the following categories:• Capital costs for land acquisition, civil works, equipment procurement and installation.
• Engineering and design costs include fees for engineering and design services, including process engineering, plant layout, and equipment design.
• Labor costs related to skilled and unskilled labour required for plant construction, equipment installation, and commissioning activities.
• Permitting and regulatory compliance costs include fees associated with obtaining permits, environmental impact assessments, and complying with regulations.
• Utility costs for power supply, water supply, wastewater treatment, and other utilities required for mineral fertilizer plant operation.
• Operational costs for raw material procurement, maintenance, labor, utilities, packaging, marketing, and finished products distribution.
It is recommended to engage with engineering firms and professional contractors who can provide detailed cost estimates based on your specific project requirements and location. A comprehensive feasibility study and detailed project planning are crucial to accurately assess the cost factors specific to a mineral fertilizer plant project.
The largest projects of mineral fertilizer plants in the last decade
In recent years, investment in the construction of fertilizer plants around the world continues to be at a very high level.This is due to the growing population and the high need for the production of affordable food and agricultural products of various types. Investments in the production of mineral fertilizers remain attractive for many companies and financial institutions.
As an example, several major projects of the last decade can be cited:
1. Ma'aden Wa'ad Al-Shamal Phosphate Project launched in 2011 was a large-scale phosphate mining and processing complex located in the northern part of Saudi Arabia. This expensive project, which included an ammonia plant, an integrated phosphate complex, and supporting infrastructure, was estimated to cost up to $8 billion.
2. BHP Billiton's Jansen Potash Project. Although construction of the Jansen Potash Project in Saskatchewan, Canada, started in 2008 and continued beyond 2019, it is worth mentioning due to its enormous estimated cost. The project, which involves the development of a large-scale underground potash mine and processing facilities, is expected to have a total investment of over $14 billion upon completion.
3. Donaldsonville Nitrogen Complex Expansion, US. CF Industries in 2016 expanded its Donaldsonville nitrogen facility in Louisiana, which included the construction of new ammonia and urea plants. The expansion project had a price tag of $2.1 billion.
4. Indorama Eleme Fertilizer Plant, Nigeria (2016). The Indorama Eleme Fertilizer Plant, located in Port Harcourt, was a major ammonia-urea complex constructed by Indorama Corporation. The project's cost was reported to be around $1.5 billion.
Saudi Arabia, China, Brazil, Russia, India, Canada, Australia, Kazakhstan, Morocco and the United States of America are among the countries that are implementing the largest investment projects for the construction of mineral fertilizer plants. The scale and cost of such investment projects usually require the development of highly efficient financial models built on the basis of borrowed capital.
If you are interested in raising large funds based on project finance or long-term loans issued by private investors / investment funds, please contact our financial team for details.
GCAM Investment Group has been contributing to the financing of large projects in the production of mineral fertilizers, the chemical industry and related fields for a long time.