After receiving the necessary documents and project presentation, our team will try to review your request as soon as possible, and leading experts will offer the best options for project funding.
- Municipal solid waste treatment plants: structure and principles of operation
- Construction of solid waste sorting lines
- Equipment for crushing and compacting solid waste
- Construction of plastic recycling plants
- Construction of plants for the processing of paper and cardboard
- Construction of food waste processing plants
- Construction and demolition waste recycling plants
- Construction of car recycling plants
- Construction of plants for the processing of waste electrical and electronic equipment
- Construction of RDF processing plants
- Construction of waste processing plants under an EPC contract
More than 2 billion tons of municipal solid waste (MSW) are generated annually in the world.
According to a study by the World Bank, by 2050, the annual amount of waste will increase by 70%, reaching 3.4 billion tons.
In low-income countries, this figure will triple due to rapid economic growth.
Better waste management, including the efficient recovery of valuable materials, is now the key to human health and safety, as well as a well-being of the environment and sustainable growth.
Solid waste production in different regions of the world (million tons per year) *:
Region of the world | 2016 | 2030 | 2050 |
Middle East and North Africa | 129 | 177 | 255 |
Sub-Saharan Africa | 174 | 259 | 516 |
Latin America and the Caribbean | 231 | 290 | 396 |
North America | 289 | 342 | 396 |
South Asia | 334 | 466 | 661 |
Europe and Central Asia | 392 | 440 | 490 |
East Asia and the Pacific | 468 | 602 | 714 |
* - statistical information and forecasts of the World Bank.
Recycling saves a lot of resources, both materials and energy.
The construction of waste processing plants around the world is helping to solve the growing problem of pollution and depletion of natural resources. Moreover, recycling is a lucrative business with great prospects.
Over the years, we have funded many environmental and other projects around the planet.
Together with our partners, we offer financing and construction waste recycling plants, landfills, water and wastewater treatment plants and many other facilities.
Municipal solid waste treatment plants: structure and principles of operation
The accumulation of MSW is considered a sign of inefficient production and unsustainable consumption habits.This is a serious problem for the economy and the environment.
Today, the construction of municipal solid waste treatment plants is becoming a major social problem that needs to be addressed, as is the proper sorting of waste that is generated daily in cities. The challenge for the future is to use resources separated from waste more efficiently and reduce the environmental impact, which implies improved waste management.
Municipal solid waste treatment plants technology and equipment
Modern MSW processing plants differ significantly in their design features.During the construction of each facility, it is important to consider the type and amount of incoming waste, the purpose of processing, the possibility of selling recovered components, etc.
Mechanical processing involves the use of a variety of equipment for separating, crushing, sorting and compacting waste. These processes increase the efficiency of pre-processing and allow for the further separation of recyclable materials.
A solid waste processing line usually consists of the following elements:
• Package openers.
• Sorting drums.
• Pneumatic separators.
• Ballistic separators.
• Electromagnetic separators.
• Bio-drums for drying waste.
• Presses for compaction, etc.
In each case, the process line must be designed taking into account the type and composition of the waste to be processed, as well as the customer's requirements for the quality of the product and the budget of the particular project.
During the construction of a waste processing plant, an individual set of equipment is selected, adapted to the needs of your business.
Construction of solid waste sorting lines
The mixed city waste stream is of little value, but some of the materials it contains can be recovered and replaced with raw materials in production, increasing business profitability.Modern mechanical sorting makes it possible to separate ferrous and non-ferrous metals, light fractions, plastic, glass and other components from the waste stream. In this regard, sorting lines serve as a kind of filter between the stages of collection and disposal of solid waste.
The configuration of sorting lines, the efficiency of the selected process and the quality of the materials obtained are determined by the characteristics and composition of the collected waste. Collection and sorting systems should be designed to maximize material recovery rates.
Municipal solid waste sorting lines typically include a number of processes and sorting machines, as well as ancillary equipment to control and improve the quality of the resulting products. Waste in sorting equipment goes through a series of processes to recover valuable components and remove unnecessary materials for disposal or incineration.
Metals, glass and contaminated plastics must be separated efficiently in sorting lines. Waste sent to waste processing plants is overly mixed during collection, which usually does not allow high-quality processing with 100% yield.
When constructing waste processing plants, it is necessary to take into account the needs of the customer.
What materials to recover?
What types of waste do you plan to receive from suppliers?
What investment costs does the customer expect?
Depending on the quality of sorting, the resulting products can be directly fed into various production processes or sent for additional fine sorting. There is no precise definition of the mixture of components suitable for dry processing, but this list usually includes ferrous and non-ferrous metals, glass and plastics, which are especially easy to separate.
Plastics and metals can also be picked up with paper and cardboard, although some contamination can be expected in these cases. Glass is usually not collected with paper and cardboard, as glass particles seriously reduce the recyclability of paper products and can damage equipment.
When deciding to invest in a new MSW sorting line, there is a number of factors to consider.
In addition to economic, legal and infrastructural considerations, some technical considerations need to be considered in order to ensure the viability of a waste processing plant project.
General approaches to sorting solid waste
There are two different conceptual approaches to sorting solid waste:• Positive sorting aims to identify and remove the desired fraction from the stream (eg eddy current separator for separating non-ferrous metals).
• Negative sorting aims to remove unwanted materials from the general waste stream (eg separating plastic bottles).
It can be summarized that positive sorting of solid waste leads to obtaining high quality products with low productivity, while negative sorting is characterized by high productivity and low quality of recovered materials.
Both approaches can be used on the same sorting line. For example, manual removal of unwanted materials at the beginning of the process (negative sorting) followed by automatic removal of the valuable components (positive sorting) and an additional cycle of manual removal of residual impurities at the end of the process (negative sorting) to ensure high product quality.
Manual or automatic sorting?
There are two ways of sorting municipal solid waste – manual sorting and automatic (mechanical) sorting.When constructing waste processing plants, consideration should be given to the type and rate of incoming waste, business goals and the ability to sell certain recovered materials with certain characteristics.
Developed countries tend to use advanced sorting technology, while developing countries may have simple solutions suitable in terms of labor and maintenance costs.
Factors to consider when choosing a method for sorting solid waste:
• Economic requirements.
• Technical characteristics of the sorting line.
• Features of incoming solid waste streams.
• Requirements for equipment repair and maintenance.
• Environmental, health and safety aspects.
• Initial investment in the project.
A combination of manual and automatic methods is most commonly used in sorting lines.
Manual sorting is suitable for some stages of the process, while in other stages it is more appropriate to use targeted, safe and cost-effective automation. This is especially true for large waste processing plants that receive large volumes of recyclable materials from commercial and industrial sources.
For quality control at the end of the process, laborious manual sorting is used to ensure that the separated fractions meet specifications.
Manual methods are also used to pre-sort incoming materials. In this way, unwanted or contaminated materials are removed, allowing the plant to increase the efficiency of subsequent highly automated systems.
The successful application of automated sorting of solid waste depends on the compatibility of each waste stream with certain technologies. It is important to choose the right technology for each stage of the sorting process so that one material is handled differently than the others.
Modern technologies for sorting solid waste
The composition of solid waste determines the stages and technologies used.Solid waste is becoming an increasingly complex mixture of materials every year, requiring more sophisticated sorting technologies to recover pure materials. These technologies must be able to sort a wide range of materials regardless of particle size, moisture content and degree of contamination.
Growing differences in waste streams usually necessitate a combination of several technologies for waste separation. These differences must be taken into account during the construction phase of the waste recycling plant.
The main technologies for sorting solid waste currently include:
• Screening: drum, disc and oscillating screens.
• Separation by air: zigzag, rotary and countercurrent sorters.
• Ballistic separation, magnetic separation, eddy current separation, etc.
Waste processing plants use different sensor technologies:
• NIR (Near Infrared Spectroscopy) for the separation of plastics such as polyethylene terephthalate, high density polyethylene, polyvinyl chloride, PVC, polystyrene, etc.
• EMS (Electromagnetic Sensors) for identifying metals by their conductivity.
• VIS (Visible Field Spectroscopy) for the identification of colored materials.
• XRT (X-ray Transmission) to determine the atomic density of waste.
• XRF (X-ray Fluorescence) for sorting metals / alloys.
Robotic waste sorting technologies significantly increase the efficiency of sorting some waste.
They are extremely useful in recycling waste streams that contain hazardous materials, as they allow fine sorting without human intervention.
Typically, hazardous solid waste is passed through visible-sector cameras, near-infrared cameras, 3D laser scanners, and metal sensors, while robotic arms work on the line to remove identified materials from the stream.
One of the advantages of robotic sorting is the ability to separate several fractions at once.
The technology is still under development and is currently aimed at sorting construction waste. Many engineering companies that offer waste processing plant construction are now offering customers new sensor technologies that provide greater accuracy in identifying materials in waste streams.
One of the latest advances in this area is the use of radio frequency identification (RFID), which makes it easy to identify and classify individual packages. The concept provides for the installation of RFID tags in the packaging of various waste, which can be read after the packages arrive at the sorting point. Among the main barriers to widespread adoption of this technology are the high cost as well as the polluting effect of the RFID tag itself.
Equipment for crushing and compacting solid waste
Engineering companies should consider the following factors when selecting equipment to reduce the amount of solid waste:• Physical characteristics of the material: particle size, hardness, etc.
• Future use of the material and the need for additional processing.
• Required product properties: particle size, density, etc.
A variety of equipment is used in the construction of waste processing plants, including hammer crushers, drum mills, jaw crushers, impact crushers, roller crushers, hydraulic presses, etc.
Types of waste crushing equipment
The various types of hammer crushers differ mainly in the rotor design.They are usually used as ancillary equipment to reduce the volume of vehicle bodies, as well as construction and household waste.
They are equipped with a horizontal or vertical shaft with hammers.
Vertical hammer crushers are mainly used for the processing of municipal solid waste and light materials such as plastic and paper. The granulometric composition of the material obtained after processing depends on the number of hammers in the crusher. A special type of hammer crusher is a construction waste crusher with a horizontal conveyor line that moves heavy debris to a shaft with hammers at the end.
Impact crushers consist of a rapidly rotating shaft with replaceable hammers and crushing plates located above it. The distance between hammers and plates, as well as the inclination of the plates, can be adjusted. If stubborn material enters the crusher, the operator can lift the platen to push the waste down. Impact crushers are loaded from the top and already processed material comes out from the bottom.
Impact crushers are designed to keep material in the crushing cycle until the desired particle size is reached. When using an impact crusher to crush construction waste, it is important that the rebar is pre-removed to prevent it from wrapping around the rotor and causing equipment damage.
Compared to high-speed hammer crushers (up to 1200 rpm), roller crushers run much slower (up to 60 rpm). They consist of one or two horizontal shafts. The shafts rotate in the opposite direction to the blade, and the degree of shredding of the waste depends on the distance between the blades.
When building plants for the recycling of cars and other bulky waste, it is recommended to install hydraulic presses that press the waste against the knives.
Roller crushers are not suitable for large scrap metal and high strength materials.
To ensure efficient shredding of solid waste, bulky elements and high strength materials must be removed. The most effective particle size control is achieved with fast rotating perforated bottom drum crushers. However, the main problem with such equipment is the abrasive effect of waste on the machine itself. Therefore, rotary drum crushers are more often used for crushing plastic.
In the engineering design of waste processing lines for composting, special crushers are sometimes used, consisting of grinding teeth and sieves with a hole diameter of up to 4-5 centimeters. High-strength materials are attached to the teeth and are pushed out of the rotating arm. This equipment is rarely used due to its lower efficiency compared to hammer crushers.
Jaw crushers are commonly used for crushing hard and brittle materials. Waste is loaded from the top side between two movable cheeks, which easily break any solid particles.
In most cases, these machines are used for crushing construction waste.
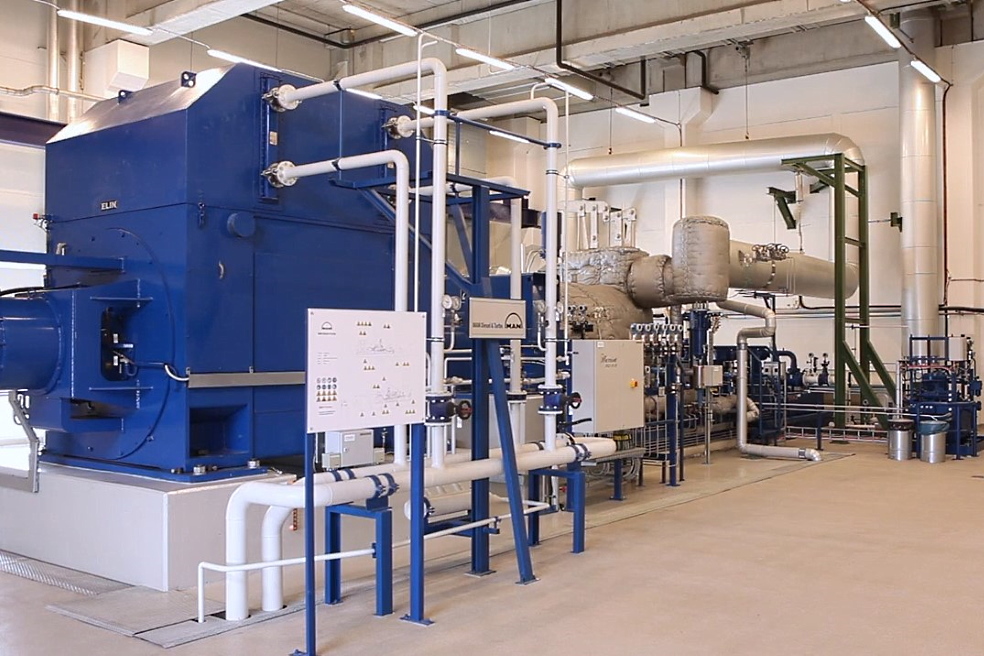
Waste compaction equipment
Construction of a waste processing plant requires the selection of the most efficient waste compaction technology so that the recovered material takes up less space.Compaction of waste is extremely important from a logistic point of view, as it significantly reduces the cost of transporting and storing materials. Another advantage is the increase in the specific energy of waste destined for energy production (incineration).
The main purpose of compacting waste is to reduce surface area and increase bulk density.
For this, two fundamentally different technologies are used:
• The crushed materials are mixed with special adhesives after drying.
• The mechanical compaction is carried out by applying an external force.
Waste compaction equipment includes presses, compactors and extruders.
The presses are used for various types of waste, including paper, cardboard, plastic packaging, etc. The choice of processing equipment depends on the customer's requirements, the type and composition of the material.
Construction of plastic recycling plants
Economic growth, along with changing consumption and production patterns, is leading to a rapid increase in the amount of plastic waste around the world.Annual plastic consumption has increased from 5 million tonnes in the 1950s to over 100 million tonnes.
After food and paper, plastic is the most important component of municipal and industrial waste. Even communities with low levels of economic development generate large volumes of plastic waste due to the widespread use of packaging, bags, PET bottles and other plastic products.
This is a serious problem for the local authorities responsible for waste disposal. Often, due to the lack of an integrated recycling system, plastic is not collected and recycled appropriately, causing disastrous impacts on the environment and human health.
The construction of plastic recycling plants opens up new opportunities for the environmentally friendly processing of plastic and its transformation into a valuable resource.
In most cases, this is economically beneficial because a lot of valuable raw materials and energy are produced.
For example, recycling plastic waste into diesel fuel not only saves resources, but also reduces greenhouse gas emissions. This is especially important in regions where industrialization and economic development place strong pressure on the environment and natural resources.
Using plastic waste as fuel
Plastic waste is one of the most promising resources for fuel production due to its high calorific value and its ever-increasing availability.Unlike paper and wood, plastic does not absorb much water, and its moisture content is much lower compared to biomass and food waste.
The choice of equipment for the conversion of plastic waste to fuel is determined by the type of base material and the properties of other waste that may be involved in the process. Effective conversion requires the selection of an appropriate technology that meets local economic, environmental and technical conditions.
Generally, non-hazardous combustible raw materials are required to produce fuel from plastic waste.
However, the composition of the plastic waste stream varies greatly and some components may contain undesirable substances.
The following substances require special attention:
• Fire retardants.
• Halogenated derivatives.
• Complex nitrogenous compounds.
• Sulfur compounds, etc.
The choice of technology, pre-treatment requirements, fuel quality, composition of waste gases and slags, as well as the possibility of chemical corrosion of equipment depend on the type of plastic.
Production of solid fuel from plastic
Plants produce two types of fuel from waste – RDF and RPF (compacted paper and plastic fuel).The first type is made mainly from food waste, paper, wood waste and plastic.
Due to the presence of food waste, drying is required before processing to remove moisture, which prevents the waste from solidifying in the desired shape and density.
RPF is made from waste paper, plastic and other dry materials. Thermoplastics play a key role as a binder for other components, such as thermosetting polymers, from which granules or briquettes cannot otherwise be formed. Solid fuels require a minimum of 15% thermoplastics, but 50% or more can cause problems during pelletizing.
RPF fuel components are usually recovered from industrial waste, but they can also be recovered from sorted municipal waste. In both cases, the plastics content will vary depending on the needs of the end user.
The shape of the fuel briquettes is determined by the equipment used.
The most commonly used screw extruders produce cylindrical briquettes.
The calorific value of RPF is easy to control as waste processing plants typically use dry and separately collected plastic, paper and other combustible waste. The resulting fuel from paper and plastic 1: 1 has a heating value of about 7000 kcal / kg.
If the solid waste stream includes plastic containing nitrogen, halogens, sulfur and other hazardous substances, the process leads to air and soil pollution due to the release of toxic gases and ash. The challenge for engineers in each case is to optimize the production line for a specific type of waste.
Production of liquid fuels from plastic waste
Only a few types of thermoplastics can be thermally decomposed to produce liquid hydrocarbons for liquid fuel production.It is preferable to use polyethylene, polypropylene and polystyrene as raw materials.
The addition of thermosetting plastics, wood and paper slows down the process speed and interferes with the recovery of liquid products. Depending on the components of the plastic waste used, the resulting liquid fuel may also contain harmful substances such as amines, alcohols, paraffinic hydrocarbons and some inorganic substances.
Liquid fuels from plastic waste can be used as a replacement for gasoline, diesel and fuel oil. They often contain various additives to improve burner or engine performance. The properties of this fuel, such as viscosity and ash content, must be tailored to the requirements of specific consumers.
During the construction of plants for the production of liquid fuel from plastic waste, plastic pyrolysis technologies are used with the subsequent condensation of hydrocarbons.
The resulting hydrocarbon mixture (pyrolysis oil) undergoes continuous distillation when the plastics in the reactor decompose sufficiently to evaporate at a certain temperature.
The evaporated oil undergoes additional cracking.
After the hydrocarbons are removed from the reactor, high boiling point hydrocarbons (diesel, kerosene and gasoline) are collected in a water-cooled condenser. The liquid hydrocarbons obtained in this way are stored in a receiving tank. Gaseous hydrocarbons such as methane, ethane, propylene and butane cannot condense and are therefore burnt in the flare stack.
Depending on the type of waste, raw materials can be fed to the reactor in different ways. Soft materials such as foil and bags are often pre-shredded and melted because they would otherwise take up most of the reactor volume. Furnaces and rotating reactors are used to carry out this process. Hydrocarbon deposits are removed from the walls of the reactor using agitators and separated.
The task of the engineering company, which is responsible for the engineering design and construction of the waste processing plant, is to ensure the most efficient, economical and safe production of fuel, taking into account the type and properties of the plastic.
Production of gaseous fuels from plastic
There are two types of gaseous fuels recovered from plastic waste:• Traditional gaseous hydrocarbons: methane, ethane, etc.
• Synthesis gas containing hydrogen and carbon monoxide.
Waste processing plants use thermal decomposition technology in reactors in their processes for the production of gaseous fuels from plastic waste.
As a result of this cycle, gaseous fuel is released as a by-product (about 20% by weight).
Gaseous hydrocarbons are produced after prolonged decomposition in a reactor at a specific temperature under strictly controlled conditions. They can be used to produce methane and hydrogen.
The technology includes the stages of pretreatment, gasification, purification and storage of gas.
Polyethylene and polypropylene thermally decompose at high temperatures in an inert atmosphere to a mixture of gaseous hydrocarbons, methane, ethane, ethylene, propane, propylene, and various butane and butene isomers. Gasification of other organic substances leads to synthesis gas.
The calorific value of gaseous products varies widely and is determined by the type of plastic waste used, the nitrogen content in the air and other factors. The heating value of synthesis gas has been found to lie between the well-known biogas and liquefied natural gas (LNG).
The construction of plastic recycling plants often involves this process, which allows companies to obtain significant amounts of valuable fuel and increases the profits of waste processing plants.

Other uses for plastic waste
It is common practice to use waste plastics as fuel for blast furnaces in the steel industry.The main requirement is that the waste must be of stable quality and free of chlorine and other substances that can degrade the characteristics of the steel being produced.
Shredded plastic waste can be used as fuel for kilns in cement plants. In this case, pretreatment is also required to remove chlorine-containing components, seal and reduce the volume. In the case of expanded polystyrene, this is achieved by melting or dissolving.
An alternative to recycling plastic waste is incineration in municipal waste incinerators to generate steam and hot water.
However, the generated energy must be used immediately for the company's own needs or for supplying nearby consumers.
Whatever the concept of your enterprise, our engineers are ready to find the best way to implement the most ambitious business ideas. Recycling plastics, MSW or industrial waste – our cutting edge technologies used in the construction of waste processing plants provide the highest economic performance for every project.
Construction of plants for the processing of paper and cardboard
Paper is one of the most widely used materials. Available in a variety of shapes and colors, paper and paperboard products are used for a wide variety of purposes.However, its widespread use also poses serious environmental problems.
From the moment the paper sheet was made to the present day, the raw materials used for the primary production of paper have been cotton, straw, sugarcane waste, flax, bamboo, timber, hemp and other natural sources.
Today, the main raw materials for the pulp and paper industry are wood and recycled paper waste. Wood for papermaking is usually obtained from conifers, including spruce, pine, etc. You can also use wood waste that is not suitable for other purposes.
The production of paper and paperboard is carried out by compacting cellulose-containing plant fibers.
The process, which consumes large amounts of electricity, heat and water, generates a lot of harmful emissions and waste.
The declared amount of wood used worldwide for paper production is about 20% of the total timber harvest. At the same time, it turns out that up to 40% of household waste is paper, and a significant part of it can be recycled.
Due to growing problems with the supply of wood, the share of recycled materials is constantly increasing. Data from the European Union show that about half of local paper production comes from recycled paper.
However, fibers cannot be recycled indefinitely.
It is believed that fiber can be used up to 7-8 times.
Most of the paper waste in the EU cannot be recycled due to the fact that it is dirty and does not meet European requirements.
But the benefits of recycling paper cannot be overstated. First of all, these are the benefits for the environment in the form of preserved trees and in the form of savings in energy, water and CO2 emissions. Research shows that recycling 1 ton of mixed paper can save energy equivalent to 840 liters of gasoline, while conserving about 32 tonnes of water and 17 trees.
The construction of paper and cardboard processing plants is in demand almost all over the world. Advanced technologies allow companies to get profits from recycling waste repeatedly, conserving natural resources and making a significant contribution to improving the environment.
Paper recycling technology
The technological process of recycling paper waste includes several stages.The specific technology and equipment should be selected during the construction of a waste processing plant, taking into account the type of waste and the requirements for the product.
The first step is usually the collection and transportation of waste. Waste paper collection points greatly facilitate the process and improve the quality of the finished product.
In general, the paper recycling process is not much different from the process used to make paper from virgin raw materials. The difference is that when using waste, they are pre-sorted by type with the removal of any impurities. For the production of certain types of paper, such as sanitary paper products, the paint must be completely removed.
After the waste paper is sorted, it is crushed in a mill with water and chemicals to form a thick slurry called pulp.
The resulting slurry is filtered several times to remove unwanted components such as staples, plastic, glue and others, and then cleaned again.
The production equipment used includes fine meshes, centrifuges and more.
To achieve the whiteness and purity of the finished paper, the ink must be removed. It is usually removed by flotation, in which air is supplied to the solution. During this process, the ink sticks to the air bubbles and rises to the surface where it is removed. After removing the ink, the slurry thickens and the remaining dyes are chemically destroyed.
If a paper recycling plant specializes in the production of white printing paper, peroxides are usually used for additional bleaching. Sulfur compounds such as sodium hydrogen sulfite can also be used.
Once the slurry is ready, it is fed to paper machines and sprayed onto wide plates. The water is then drained, the fibers are bound together to form a water-based paper. This intermediate product passes through presses to remove most of the water and is then fed to heated rolls for final drying. The dried sheets of paper are curled or cut.
Paper production has a significant impact on the environment. In turn, the waste paper recycling process also has disadvantages.
This is due to the release of a large amount of waste such as ink, alkalis, fillers and so on. But in general, the environmental effect of processing is positive.
Construction of food waste processing plants
Intensive agriculture and food production all over the world generate huge amounts of by-products and waste.Typically, the food industry releases a significant amount of biodegradable waste, including wastewater and residues with high biochemical and chemical oxygen demand. Their uncontrolled decomposition leads to the release of methane and other environmentally harmful compounds.
In Europe alone, more than 220 million tons of food waste is disposed of annually. Due to rising environmental standards, food manufacturers are now facing demands to reduce waste. This problem contributes to an increase in the cost of disposing and processing food and agricultural waste.
The largest amount of waste and by-products is generated during the processing of fruits and vegetables, meat and fish, as well as in the production of cheese and sugar.
Valuable compounds from these products can be recovered in the following ways:
• Hydrolysis.
• Distillation.
• Extraction.
• Absorption.
• Ion exchange.
• Evaporation.
• Crystallization.
• Enzymatic processing.
• Drying of residues, etc.
When constructing food waste processing plants, engineering companies take into account the specific type of waste that the customer is going to receive.
The type and volume of waste determines the choice of the most efficient technologies.
Over the past several decades, biomass has been of significant interest for the production of clean energy, and serious efforts are being made in this direction. Biological waste from the food industry and agriculture can be converted into an energy resource by various thermochemical, biochemical, mechanical, chemical or electrochemical methods.
Thermochemical and biochemical technologies are suitable for a wide range of waste, while other methods require raw materials to meet stringent requirements. Thermochemical processes occur at high temperatures in environments with different oxygen concentrations. This category includes incineration, pyrolysis or gasification applicable to relatively dry plant waste.
In biochemical technologies, such as anaerobic digestion or ethanol fermentation, special types of microorganisms convert waste into biofuel.
These methods are more applicable to food waste with a high moisture content.
Composting
Composting is an aerobic process in which organic food or agricultural waste is decomposed into nutrient-rich compost, which improves soil properties.The most suitable methods are composting in silos, concrete chambers or other similar structures, in which defined values of temperature, humidity and oxygen are maintained.
The composted material obtained as a result of a multi-stage process is sieved to remove any impurities and isolate valuable products for various purposes.
Fermentation
During fermentation, sugar-containing food waste is converted to ethanol by certain types of microorganisms.The process is usually anaerobic, but it can also be done under aerobic conditions.
The reactors used for fermentation can be operated cyclically, sequentially or continuously. This technology is suitable for processing plant waste with a high sugar or starch content (e.g. sugar beet, corn, potatoes).
The technological process includes several stages:
• Hydrolysis.
• Fermentation.
• Separation.
• Cleaning.
If lignocellulosic waste is used, pre-treatment by grinding and acidic or enzymatic hydrolysis is required.
Fermentation process conditions such as temperature, humidity and pH must be optimal for the growth of a particular microorganism.
Nutrient deficiencies can lead to decreased ethanol yield. Microorganisms need several nutrients and nutrients with micro-concentration (carbon, hydrogen, phosphorus, sulfur, vitamins, potassium, and calcium). All these features are taken into account when developing technology.
Anaerobic digestion
The biochemical process, in which biogas is produced from organic materials, is suitable for food waste generated by producers and end users, as well as for wastewater and biological by-products from agriculture.Anaerobic digestion takes place in a bioreactor that operates in dry or wet conditions. When building food waste processing plants, mesophilic (35 ° C) and thermophilic (55 ° C) reactors can be installed. The advantage of thermophilic biogas reactors is a shorter processing time. On the other hand, maintaining a high temperature requires more electricity.
Also, engineers must solve the problem of increasing the concentration of valuable substances, sterilization and special treatment of waste to produce a high-quality product.
The process of anaerobic digestion has four main steps:
• Hydrolysis.
• Acidogenesis.
• Acetogenesis.
• Methanogenesis.
During hydrolysis, the insoluble organic matter in the reactor is converted into a soluble form.
Acidogenesis produces acetate, volatile fatty acids, carbon dioxide and hydrogen. The volatile acids are then decomposed into acetate and hydrogen during acetogenesis. At the last stage, methane and CO2 are obtained from acetate and hydrogen.
The final product (biogas) is used for cogeneration of heat and power in CHP plants. In addition, biogas can be purified and then used as fuel for vehicles.
Pyrolysis
During pyrolysis, food or agricultural waste is heated to a high temperature without oxygen, resulting in the release of gases, oil, coal.During pyrolysis, large hydrocarbon molecules (cellulose, hemicellulose and part of the lignin) break down into lighter ones.
Pyrolysis can be classified as slow or fast.
With slow pyrolysis, food waste is heated in a reactor to 400 ° C and above, and the processing time increases.
The result is more oil and coal and less gas.
The goal of fast pyrolysis is to maximize the release of liquid and gaseous products by quickly heating food waste to a suitable temperature (above 650 ° C). The most commonly used pyrolysis reactors have a fixed, mobile, fluidized or circulating bed.
When designing pyrolysis equipment, the properties of the waste should be taken into account. For example, the high content of potassium in the waste promotes corrosion of the metal elements of the reactor, therefore the equipment requires special protection.
In addition, too high a moisture content can slow down the process and lead to increased energy consumption. The specific ratio of hydrogen and carbon in waste also affects the yield of useful products.
Gasification
Gasification involves the partial oxidation of waste at high temperatures to a gas mixture known as synthesis gas.Most suitable for this process are lignocellulosic materials, as well as some agricultural waste.
A typical gasification process includes:
• Drying.
• Waste pyrolysis.
• Oxidation of intermediate products.
• Recovery of valuable substances.
The efficiency of the gasification process depends on many factors such as waste particle size, moisture content, pressure, heating rate, temperature and residence time of the waste in the gasifier.
To ensure optimal results, engineering companies practice a comprehensive approach to the construction of waste processing plants.
What kind of waste will be received?
What is the initial investment planned by the customer?
What products does the company intend to produce?
Answers to these questions are the key to the successful implementation of an investment project.
Construction and demolition waste recycling plants
Construction and Demolition Waste (C&DW) is one of the heaviest and largest waste streams generated in the European Union.They are responsible for about 25-30% of the total waste in the EU and include numerous materials: concrete, brick, gypsum, wood, glass, metals, plastics, solvents, asbestos, and excavated soil. Many of these components can be recycled.
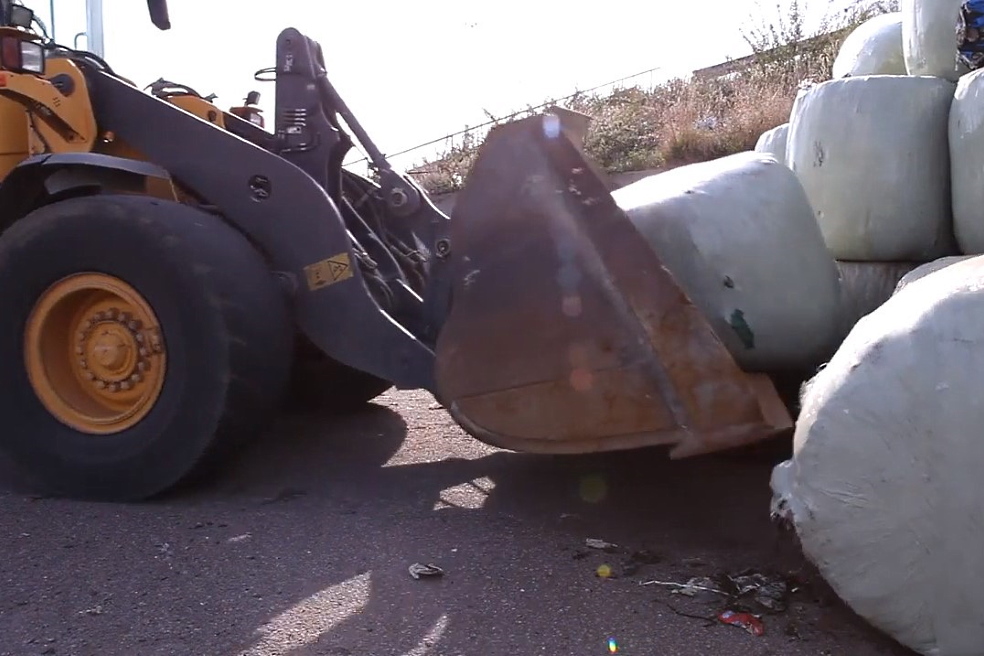
C&DW are formed from activities such as the construction and demolition of buildings and urban infrastructure, including road construction and repair.
Significant differences in terms make it difficult to compare the volume of waste recycling between countries.
The potential for recycling and re-using construction and demolition waste is enormous, as their components are usually expensive. There is an extensive market for secondary materials used in the construction of roads, drainage systems and other facilities. C&DW separation and recovery technology is available and usually does not require a large investment.
Despite the large investment opportunities, the percentage of recycling and recovery of construction waste in the EU varies widely (from 10 to 90%). If sorting is not used on construction sites, C&DW stream can contain hazardous components that pose environmental risks and complicate recycling.
Today the construction of C&DW recycling plants is a complex technical task that requires significant practical experience and advanced technologies from the engineering company.
Knowledge of the characteristics and types of waste contributes to the efficiency of sorting and improves the quality of processing. It is especially important to take into account the specifics of various types of hazardous waste and their impact on the environment.
Processing of stone, brick and concrete waste
Crushed stone, concrete and brick make up the bulk of the waste associated with the construction and renovation of buildings, engineering structures and roads.Disposal of such waste is usually carried out by separating and shredding useful materials.
This type of waste becomes the basis for the creation of aggregates and other products.
Demolition stone and similar materials can also be crushed and used as aggregates. Construction of aggregate plants is gaining momentum and the use of C&DW is very beneficial in this industry.
Concrete is one of the most common types of construction waste. This is not surprising since concrete structures are most often used in modern construction and renovation. Almost every construction project involves the dismantling of concrete structures as one of the main initial activities, so the need for concrete processing is growing.
The practice of European countries such as the Netherlands and Denmark, where there is a shortage of natural stone materials, shows that recycled concrete-based aggregates can be used to produce high-strength materials.
For this purpose, it is important to essentially basic processing technology (crushing, screening) and to increase the efficiency of sorting concrete waste before processing.
Recycling of asphalt concrete
During the repair and maintenance of the road surface, a huge amount of asphalt concrete is produced.Asphalt concrete is also a type of recyclable construction waste.
There are two technologies for on-site processing of asphalt concrete:
• Hot recycling. Using special portable equipment, the old material is heated, after which a new hot asphalt concrete layer is applied on top.
• Cold recycling. This is one of the most effective techologies for recovering this type of construction waste. It consists in grinding asphalt in an aqueous medium with the addition of a stabilizing substance to the resulting mixture.
Recycling of asphalt concrete in special factories ensures the best results.
The road surface is removed by milling and then transported to the plant for recycling. Recycling asphalt concrete provides significant economic benefits and helps to reduce the consumption of valuable natural resources such as oil.
Ceramics recycling
As a valuable building material, ceramics have high mechanical strength.Ceramic products are recyclable and reusable. Recycled ceramics find many uses in construction, including park alley sidewalks, drainage systems, and more.
During the construction of waste processing plants, high-tech equipment is used to ensure high efficiency of recycling and obtaining a high-quality secondary product for various areas of use.
The task of engineering teams at the design stage is to optimize the technology for processing construction waste for the needs of a particular customer, taking into account the type of waste, its composition and the possibility of reuse.
Construction of car recycling plants
Car scrapping is an acute problem in developed countries.In the United States alone, up to 15 million old vehicles are scrapped every year. Environmentally friendly recycling of used vehicles is aimed at achieving a level of reuse and recycling of at least 85% of the total weight.
These requirements are established during the vehicle design phase, which is why modern car recycling plants recover a significant amount of valuable materials from each vehicle. Wherever possible, manufacturers limit the use of hazardous substances and make it easier to disassemble, reuse and recycle components.
Construction requirements for car recycling plants
The construction of car recycling plants in each country is subject to specific requirements.So, places for collection and storage of equipment should have a waterproof surface, as well as equipment for collecting oils, precipitators and degreasing devices.
Plants should have suitable storage areas for components resulting from vehicle dismantling, including storage facilities for environmentally safe storage of parts contaminated with engine oil.
They should also be equipped with suitable containers for lead-acid batteries, filters containing environmentally hazardous polychlorinated biphenyls or terphenyls; equipment for draining liquids.
Adequate storage tanks are also required for separate storage of fluids such as fuel, gear oils, coolants, antifreeze, brake fluids and other potentially hazardous liquid waste. To avoid the risk of fire due to the accumulation of large quantities of tires, they must be stored in suitable storage facilities after disassembly.
Engineering companies that build vehicle recycling plants must consider numerous requirements, including local car recycling standards.
Stages of car recycling
The processing of used vehicles takes place in several stages:• Disassembly.
• Pressing.
• Shredding.
• Recycling.
All operations for the separation and storage of components are carried out in such a way as to ensure their suitability for subsequent reuse.
Disassembly work involves separating reusable automotive parts and collecting components classified as hazardous. This includes lead-acid batteries, catalytic converters (containing platinum and rhodium), fuels, engine oils, manual and automatic transmission oils, brake fluids, hydraulic clutch fluids, and more.
Various liquids are stored in special containers or processed on appropriate processing lines.
The car disassembly process must be carried out very carefully to reduce the amount of hazardous substances in the waste during subsequent processing.
The metal remains of the car are pressed in portable and stationary hydraulic presses to take up less space for possible transportation. Sometimes portable presses are preferable, as they can be used at waste collection sites in order to reduce the cost of transporting scrap metal.
The next step is crushing the scrap metal.
For this, different types of equipment are used, in which the car body goes through several stages.
As a result, the body is crushed into pieces of several centimeters in size.
The resulting material is thoroughly processed, as a result of which ferrous metals are separated from non-ferrous ones. The non-recyclable fraction after these processes will be less than 20% of the vehicle weight.
Used car tires and their components are not hazardous and can be 100% recycled. They consist mainly of rubber (43-48%), soot (21-22%), metal (15-27%), textiles (5%). At the end of their life cycle, tires can be transformed by physical or chemical processes into a new product or raw material for other applications.
Possible applications of the obtained rubber granules or powder:
• Synthetic coatings.
• Coverings for sports grounds.
• Modification of asphalt mixtures.
• Production of conveyor belts.
• Thermoplastic elastomers.
• Activated carbon.
Automotive lead acid batteries are also recycled.
The batteries are separated and the harmful lead acid paste is extracted.
Pieces of lead and plastic are submerged in pools of water. Here, lead and other metals sink, and light plastic parts float to the surface.
Car recycling plants separate battery materials. The plastic parts are separated and a special machine blows them into the container. They are sent to the plastics processing plant. The acid from the lead acid paste is neutralized and converted to water. Lead can be used in the future for the production of new batteries.
Recycling vehicles has important economic and environmental implications.
If you are interested in financing and construction of a car recycling plant under an EPC contract, please contact our representatives at any time.
Construction of plants for the processing of waste electrical and electronic equipment
Electrical and electronic equipment is an important part of everyday life.Rapid technical development in this sector leads to a constant stream of new solutions and shorter product lifetimes.
Globally, the annual volume of waste electrical and electronic equipment (WEEE) ranges from 7 to 20 kg per person per year. The difference is caused by different understandings of this term. In the United States, the WEEE category includes only information and telecommunications equipment, and in Europe, the term also covers large appliances, refrigeration equipment, and medical devices.
Importance of WEEE recycling
Against the backdrop of a deteriorating environmental situation and a shortage of resources, the construction of new plants for the processing of waste electronic and electrical equipment today has become a priority task not only for private companies, but also for governments.WEEE contains rare metals including gold, silver, palladium and platinum, as well as potentially hazardous substances such as lead, mercury, cadmium and beryllium. Therefore, responsible handling of electronic waste should include reusing working devices, repairing damaged equipment, and properly disposing of non-recyclable components.
The first two options are the most desirable as they extend the life of the products and improve resource efficiency.
Recycling WEEE allows companies to reuse valuable metals, significantly reducing their environmental impact.
Electronic manufacturers are the main consumers of metals such as nickel and nickel alloys, cobalt alloys, titanium and titanium alloys. As raw material depletes and increases in value, investment in WEEE recycling plants is becoming an increasingly profitable solution.
In addition to recovering precious metals, WEEE recycling reduces the environmental impact of primary production. This is due to such energy-intensive stages as mining and smelting of precious and special metals, which are associated with significant emissions of carbon dioxide.
Waste electrical and electronic equipment poses a significant risk to the environment and health if not properly used. Although WEEE only accounts for 2% of landfilled waste, it contains about 70% hazardous components.
These include lead in cathode ray tubes and solders, mercury in switches, polybrominated flame retardants in printed circuit boards, plastic in housings and cables, and selenium, cadmium, chromium, cobalt, and many other contaminants.
Sorting and mechanical processing of electronic waste
During the construction of waste processing plants focused on recycling electronics waste, close attention is paid to technological lines for sorting and mechanical processing.This stage aims to separate waste streams, mainly metal, glass and plastic, which will subsequently be recycled. The complexity of pre-processing is determined by the customer's requirements for the finished product. Additional mechanical processing not only increases the cost of the process, but can also lead to significant losses of precious metals.
Complex components and devices such as printed circuit boards, mobile phones and other small household appliances are removed from the waste stream before processing. When the boards are not removed by hand or crushed, precious metals are mixed with low-value fractions such as glass and aluminum. Mixing complex components can lead to losses of up to 40% of precious metals.
After separation, the fraction of ferrous metals is sent for the extraction of iron and aluminum to furnaces, and copper alloys are usually fed to automated lines for the extraction of precious metals, copper and other non-ferrous metals.
Recovery of metals from WEEE
WEEE pyrometallurgical processing consists of melting waste electrical and electronic equipment in high-temperature furnaces.This technological process is used to recover copper and precious metals that can dissolve in copper, such as silver, gold, platinum, and palladium.
Electronic waste can be recycled into small furnaces.
Their processing into copper sulfide concentrate is common for large smelters. The process consists of several stages. The first involves separating hazardous components such as batteries, cathode ray tubes, mercury lamps, and more.
Typically, high-quality electronics waste does not go through the grinding stage, but is sent directly to the smelter. This prevents the formation of dust containing precious metals and significantly reduces the loss of metals and components in waste material streams that cannot be recovered.
Plastic components are difficult to recycle due to the fact that they contain a mixture of flame retardants, pigments, etc.
However, they can be used as fuel for smelting.
Although pyrometallurgical processing is the most common method for recovering precious metals from waste electrical and electronic equipment, this technology also has some disadvantages. These include the inability to recover aluminum and iron and the formation of dioxin emissions from the melting of halogenated flame retardants and PVC in the waste.
Over the past two decades, WEEE hydrometallurgical processing has become increasingly popular due to its high predictability, and easier process control compared to pyrometallurgical methods.
Engineering companies that build plants for the processing of waste electrical and electronic equipment develop process flow diagrams tailored to the needs of the customer.
The choice of technology is determined by the type and quantity of waste, product requirements, etc.
Construction of RDF processing plants
Typically, the production of a combustible fraction from municipal solid waste (MSW) includes two stages – waste pretreatment and recovery.This fraction, recovered from the solid waste stream, is known as RDF fuel.
In terms of composition, RDF is a mixture of substances with higher flammability (eg paper, plastic) compared to the components in the overall waste stream.
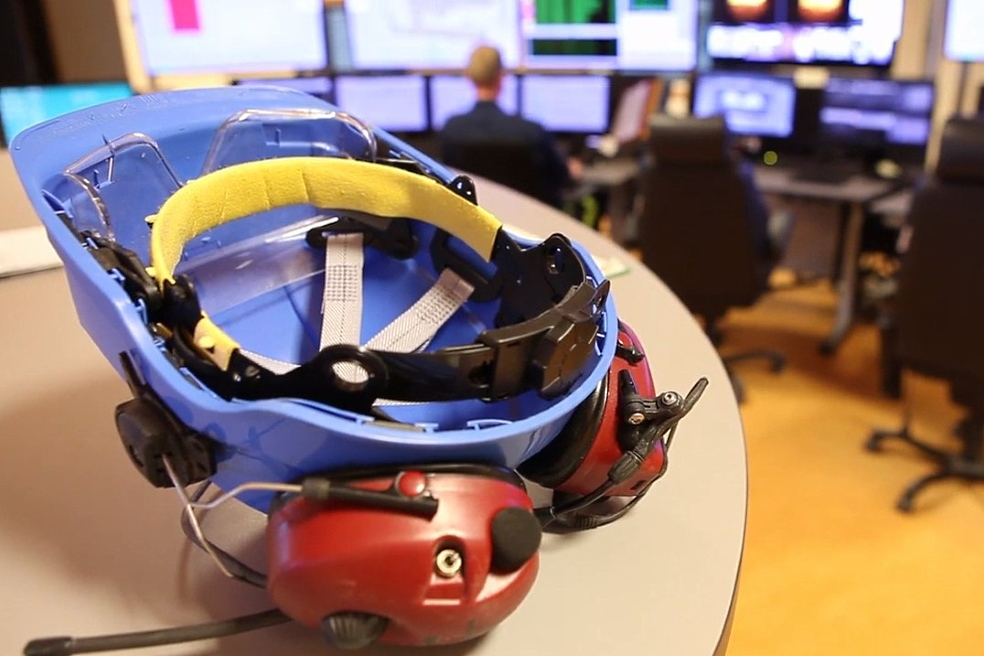
During the construction of RDF processing plants, special attention is paid to equipment for pre-processing of waste, that is, receiving solid waste directly and separating them into two fractions - combustible and non-combustible.
This process provides the starting material for the RDF production subsystem. Particle size reduction, screening and magnetic separation technologies are used to recover combustible fraction from solid waste. In some enterprises, screening precedes shredding, while in others the procedure is different.
In determining the optimal sequence of these processes, a number of factors should be considered, one of which is the composition of the waste. The pretreatment step can also include manual sorting, air sorting, and granulation.
RDF has been successfully used as a fuel additive in coal-fired boilers in thermal power plants, or as a separate fuel for specially designed boilers. It has been found that when co-fired with coal, RDF with a heating value of 12-16 kJ / g can provide up to 30% of the required energy.
Advantages of RDF fuel for the investor
This type of waste fuel is becoming an attractive investment opportunity.RDF fuel can be produced both for sale and for own consumption. For example, for heating factories.
Plants can produce RDF with different properties depending on customer requirements. One of the important characteristics of solid fuels is its calorific value, moisture content and ash content. High quality RDF has a higher heating value and lower water and ash contents.
In developing countries, where waste is usually high in moisture content, the resulting RDF will be of lower quality unless additional sophisticated treatment methods are applied. In such cases, the calorific value of the fuel can range from 11-12 kJ / g.
For ash, burning RDF can produce 4-6 times more ash than burning coal.
Therefore, even for RDF and coal co-firing systems, there must be a way to deal with the additional ash.
Although RDF contains relatively high concentrations of paper and plastic, which have a calorific value of up to 37 kJ / g, the disadvantage of RDF is the content of materials with a high ash content, which can damage boiler burners and degrade the environmental performance of exhaust gases.
For example, when high-chlorine RDF is burned, the chlorine in the fuel can form hydrogen chloride. Under certain conditions, hydrogen chloride will corrode the internal metal parts of the burner and the boiler tube.
The presence of fine metal and glass particles in RDF can lead to fuel system problems. Removing these particles is a complex technical challenge due to their specific physical and aerodynamic properties. Even with a content of less than 1%, deposits of silica and metal oxides form on the heat exchange surfaces of the boiler.
In exceptional cases, high metal content in RDF will lead to boiler failure and the need for urgent repairs.
For these reasons, the requirements for the construction of RDF processing plants are strict.
RDF production technologies
There are two ways to obtain a high-quality combustible fraction from solid waste - mechanobiological treatment and dry stabilization.In the first case, metals and solids are separated, and organic fractions are sieved for subsequent stabilization by composting with or without a decomposition phase.
The residual fraction, consisting mainly of dry paper, plastics and textiles, becomes a valuable fuel.
RDF can also be obtained by dry stabilization, in which residual waste (excluding inert and metal components) is dried and stabilized by composting. The resulting mass has a high calorific value, which makes it suitable for use as a fuel.
Pre-treatment makes it possible to extract a high-quality combustible fraction from solid waste. Careful pre-treatment ensures the production of high quality combustible fraction even when the properties of the solid waste stream change.
Screening and drying of waste
Screening is key to producing high quality RDF.Using screens with the appropriate size, small particles can be removed from the solid waste.
Since waste fines are generally inert materials with low calorific value, their removal has a double effect.
First, screening increases the total calorific value of RDF by increasing the concentration of flammable paper and plastics.
Secondly, screening significantly reduces ash content. Several studies show that about 90% of low-calorie materials can be removed with drum screen.
Another major benefit associated with pretreating waste to produce a quality fuel is the reduction in RDF moisture. This is especially important in developing countries where the waste stream is characterized by a high concentration of biodegradable materials with a high moisture content.
Depending on the climatic conditions and the design of the waste processing plant, the resulting RDF can have a moisture content about 30–50% lower than the moisture content of MSW.
As the moisture content of the fuel decreases, its calorific value increases.
Construction of waste processing plants under an EPC contract
We and our partners offer a full range of services for investors, including project finance, engineering design and turnkey construction of waste processing plants.Engineering services include:
• Planning and research.
• Preparation of all technical documentation.
• Negotiating with the authorities and obtaining official permits.
• Development, purchase and supply of equipment and materials.
• Execution of all construction and installation works.
• Testing and commissioning of the plant.
• Customer personnel training, etc.
Thanks to many years of experience in implementing large environmental projects around the world, we can offer customers advanced technologies and methods of organizing work aimed at maximum results.
Experts provide comprehensive support to customers from the drawing stage to the end of the life cycle of a waste recycling plant.
The construction of waste processing plants under the EPC contract is increasingly being used around the world.
This type of contract has a number of benefits for investors, including:
• Fixed price and completion date.
• The general contractor is fully responsible for the project.
• The customer receives exactly such an object, which is described in the contract.
• The customer should not allocate resources to interact with subcontractors.
• The construction time for large projects is significantly reduced.
Industrial, energy and infrastructure projects, implemented in many countries, are proof of professional competence and responsibility to customers.
For advice, please contact us at any time.